As the scaffolding and construction industries face a critical skills shortage, apprenticeships and workforce development remain at the forefront of industry discussions. Scaffmag spoke to Tim Balcon on apprenticeships, diversity and the skills crisis.
I had the privilege of speaking with Tim Balcon, Chief Executive of the Construction Industry Training Board (CITB), to gain insights into the initiatives and strategies being employed to address these pressing challenges.Apprenticeships: Building the Talent Pipeline
When it comes to apprenticeships, the CITB is pulling out all the stops to attract new talent into scaffolding and the broader construction industry. As Tim Balcon explains, “We’re investing in a range of initiatives to make careers in construction accessible and appealing. Our Go Construct careers portal is a prime example—it provides a comprehensive resource for individuals exploring opportunities in scaffolding and other sub-sectors.” Beyond guidance, CITB offers robust financial support to employers. “Scaffolding businesses hiring apprentices can access a £2,500 annual grant per apprentice, plus a £3,500 achievement grant upon completion,” Balcon shares. “For those pursuing the CISRS route, we fund training stages like COTS, Part 1, Part 2, and NVQ qualifications.” Despite these efforts, the scaffolding sector faces unique challenges, including what Balcon refers to as a “hidden jobs market,” where many roles go unadvertised. He believes improving the visibility of these opportunities could significantly bolster recruitment. Highlighting the scale of CITB’s commitment, Balcon notes, “Between April 2023 and March 2025, we’re investing nearly £150 million into apprenticeship grants. Since 2020, we’ve awarded over 72,000 grants, supporting employers and learners alike. Small and medium enterprises, which account for over two-thirds of construction apprenticeship starts, are particularly benefiting from these programs.” Balcon also acknowledges the need to tackle retention issues. “Currently, 60% of further education learners in construction do not end up in the industry. We need to address this by promoting the clear career benefits and providing effective recruitment and training support.”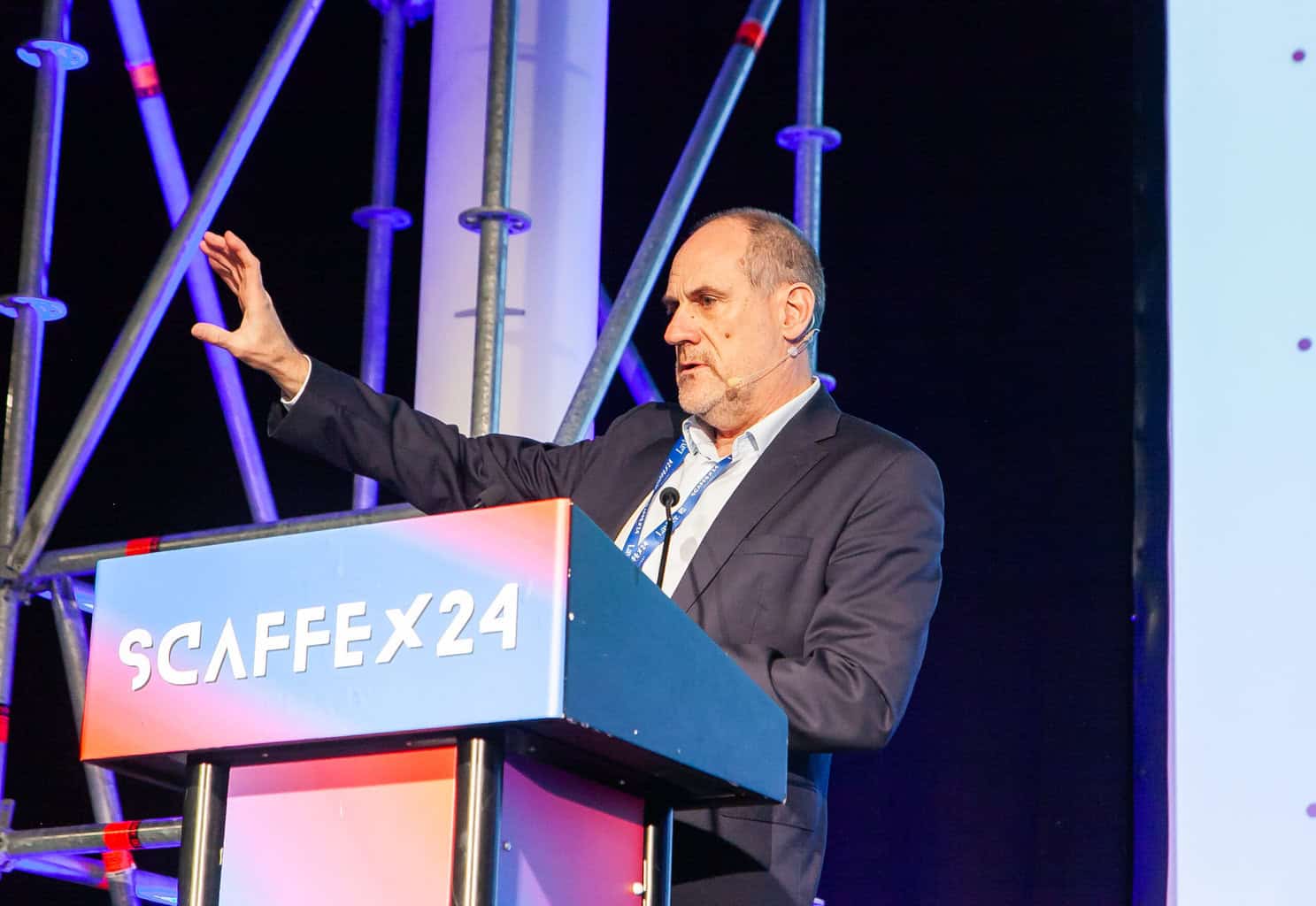
The Skills Crisis: A Collaborative Approach
The construction industry will require over 250,000 additional workers by 2028 to meet growing demand. Balcon describes this as a significant challenge but remains optimistic. “CITB has partnered with the Government and the National House Building Council (NHBC) to launch Homebuilding Skills Hubs. These hubs will deliver fast-track apprenticeships and training, enabling us to produce 5,000 new homebuilding apprenticeship starts annually once fully operational.” The initiative, which will see 32 hubs established by 2027, is part of a £140 million investment by CITB and NHBC. “These hubs are a game-changer,” Balcon explains. “They’ll flatten peaks in demand for skills and equip individuals to be productive on-site in record time.” Digital transformation is another critical area. “Technology is key to the future of scaffolding and construction,” Balcon states. “Our Industry Impact Fund provides scaffolding businesses with the financial resources to adopt digital tools that enhance productivity and safety.”Overcoming Challenges and Seizing Opportunities
Balcon outlines three core funding strategies designed to support scaffolding businesses grappling with rising training costs:- Grants: Financial support for completing construction-specific training, often covering the full cost.
- Skills and Training Fund: Tailored allowances for small businesses, providing up to £5,000 upfront to cover eligible training expenses.
- Employer Networks: Regional CITB advisors source and subsidise training on behalf of employers, covering up to 70% of costs.