Layher pioneers its advanced cantilever technique with Hardrock Scaffolding using Layher’s Under-Deck Flex Beam
A colossal scaffolding project is underway beneath the iconic Forth Road Bridge, where West Lothian-based
Hardrock Scaffolding Ltd is delivering a UK-first installation using Layher’s advanced Flex Beam launching system for contractor Millar Callaghan, working with BEAR Scotland on behalf of Transport Scotland.
Opened in 1964, the Forth Road Bridge was once the longest suspension bridge of its kind in Europe and remains a vital part of Scotland’s transport infrastructure. Now serving as a dedicated corridor for public transport, cyclists, and pedestrians, it continues to play a key role alongside the newer Queensferry Crossing and the historic Forth Rail Bridge.
Suspended 55 metres above the Firth of Forth, the latest phase of the project sees Hardrock Scaffolding deliver a highly technical hanging scaffold, providing safe access for workers refurbishing vital maintenance walkways underneath the bridge, a critical part of ongoing infrastructure upkeep.
A UK First in Non-Mechanical Cantilever Bridge Access
Erecting scaffolding beneath a bridge, particularly at such height, is no easy feat and would be a daunting prospect for many experienced scaffolding contractors. But not for Hardrock. With a proven track record in complex access solutions, the company has embraced the challenge, pushing the boundaries of what’s possible with a method that improves both safety and efficiency.
Hardrock Scaffolding embrace innovation and wastes no time utilising the
Layher UK progressive cantilever construction technique – never before deployed in the UK.
At the heart of the system is Layher’s hi-tech aluminium FlexBeam, which is being installed incrementally from a secured level using just three additional components, the game changing roller unit, a receiving bracket, and a fitting retainer — all specially designed for this innovative launch method – no requirement of chains, motors or additional supplementary launch beams – simply safe, quick, and material saving.
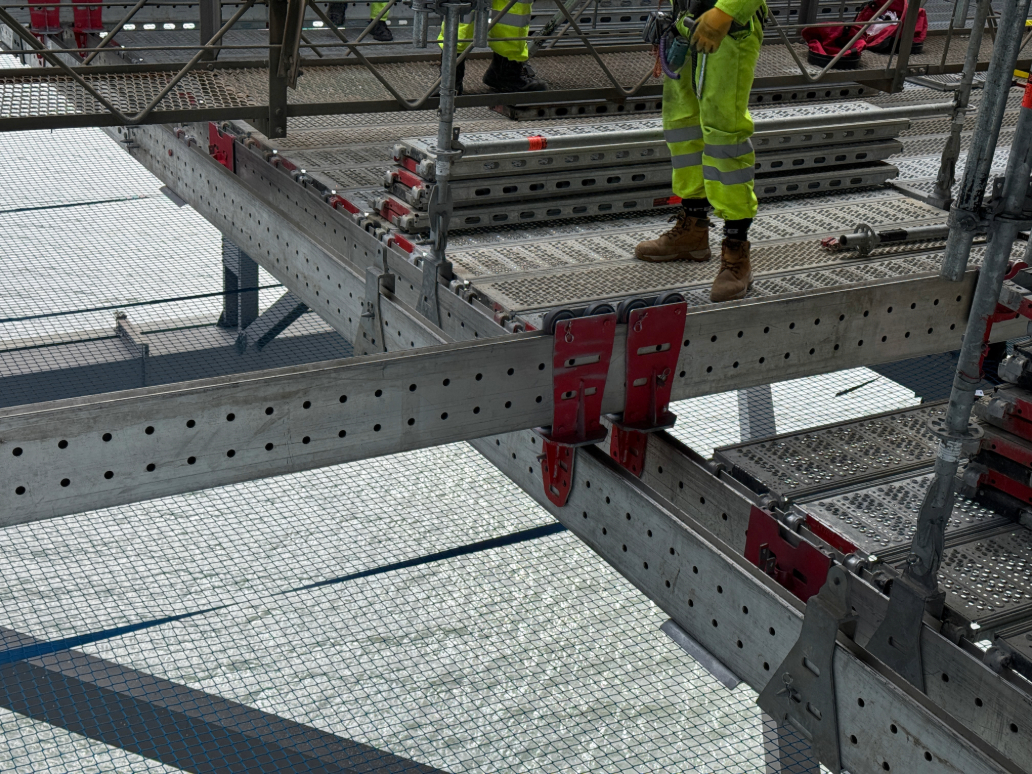
In this case, this technique allowed for a span of connected Flex Beam sections measuring 22-metres, to be moved smoothly and safely into position in seconds. The beams are pinned, not bolted, simplifying the build process and reducing reliance on tools at extreme heights.
George Brown, Hardrock’s Senior Contract Manager, said:
“Hardrock Scaffolding, working strategically with Layher UK, are always striving for safer methods of installation. When the new Flex Beam rolling launch method was shown to our dedicated bridge team, they couldn’t wait to put it into practice.
“Having already worked closely with Millar Callaghan on bridge refurbishment projects using the Layher Flex Beam, it made perfect sense for Hardrock to showcase this new method.
We’ve been genuinely impressed with how this launching system performs we were able to push out a beam line span of 22m (made up of 3 x 6m flex beams & 1 x 4m flex beam joined together) with a combined weight of 250kgs with such ease and simplicity, and then additionally deck out the area with 90 x Layher steel decks in just over 3 minutes.”
“We are proud to see one of our joint innovations between the Layher team in Scotland and Germany brought to life and perform even better than we expected in a real-life situation” said Kenneth Redman, Layher’s UK technical manager.
Step-by-Step Precision
The process begins with the installation of roller units and receiving brackets onto an already suspended scaffold structure. From there, transverse beams with pre-fitted suspension shoes are placed and secured without tools.
Using the cantilever method, scaffolders then push out the Flex Beams bay by bay, repositioning units and securing each new section with pins to maintain structural integrity.
This modular approach not only speeds up assembly and dismantling but significantly enhances worker safety, a top priority given the height and complexity of the bridge.
Raising the Standard for Infrastructure Projects
The project highlights how modern scaffolding solutions are playing an increasingly critical role in the upkeep of major infrastructure. By introducing safer, faster, and more efficient construction methods, Hardrock Scaffolding and its partners are helping to transform the delivery of essential maintenance on complex structures, such as the Forth Road Bridge.
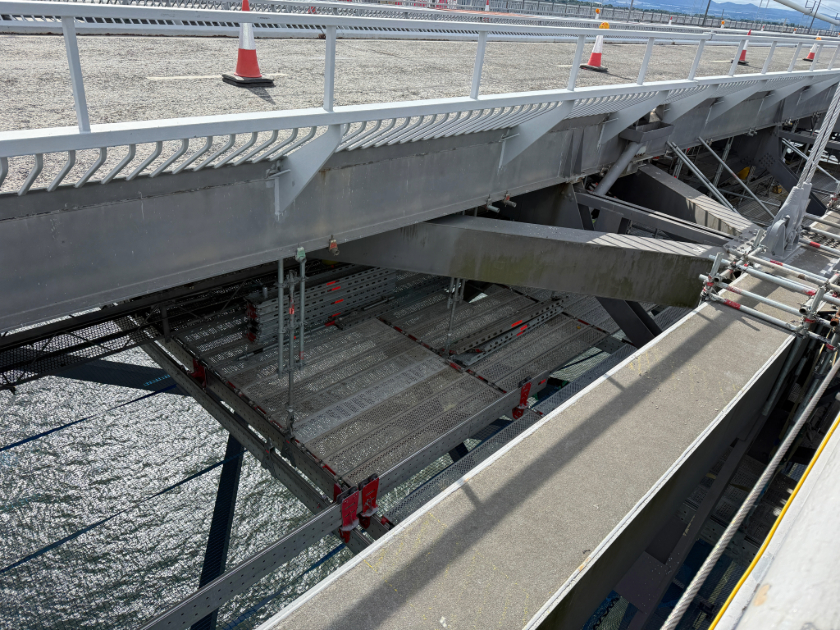
The innovative cantilever system from Layher not only reduces the risk to scaffolders working at height but also minimises disruption to the bridge’s ongoing operations, a key consideration for structures that remain in daily use by the public. Faster installation times mean less exposure for workers and greater cost-effectiveness for long-term maintenance programmes.
As infrastructure across the UK continues to age, demand for advanced access solutions is rising. Projects like this demonstrate how the combination of cutting-edge equipment, engineering expertise, and collaborative working can meet the unique challenges of maintaining critical transport links.
With this ambitious scaffold operation, Hardrock Scaffolding is not only supporting the latest phase of essential repairs but also setting a new benchmark for safety, efficiency, and technical excellence in the industry.