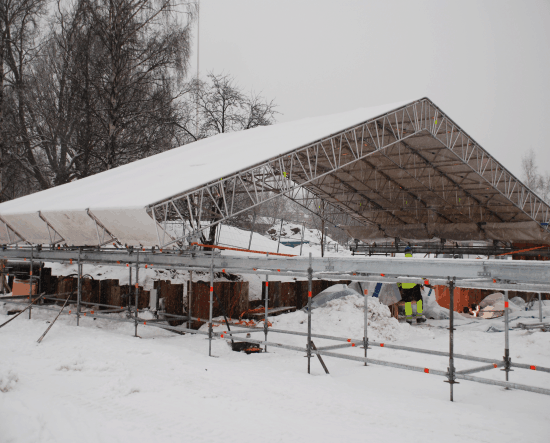
In the last few years the construction industry has had to deal with rising material costs, construction-related bankruptcies, reductions in government capital expenditure and constantly shrinking budgets. And with the world’s economy still in such a fragile state, building contractors all over the world are under pressure to deliver construction projects on budget, on time and on demand – whatever the weather.
As Europe’s largest industrial employer and generating almost 10% of the European Union’s Gross domestic product (GDP), the construction industry will inevitably play a crucial role in the economic recovery and so the pressure is on contractors to meet ever increasing demands. As a result, more and more construction projects need to be carried out during inclement weather months when bad weather would traditionally have caused huge delays.
During the 2010/11 winter period, Germany saw its construction output decline by a staggering 24%, with the slump largely attributed to heavy snowfall. And despite its 2011 recovery when the country’s economy grew by 3%, it contracted in the first quarter of 2012 – this time by 0.25%. Again, an unusually cold winter clearly had an impact – with February temperatures dropping below -20°C and causing temporary suspension of many German construction sites.
In France, it was heavy rainfall in February 2012 that forced many construction sites to suspend work – further delaying the country’s economic growth and recovery from its 2009 recession. These extreme weather conditions and fluctuating temperatures are fast becoming the norm all over Europe, and precipitation and wind speeds are also on the increase. In fact, it has been predicted in Sweden wind speeds will increase by 0.8m/s and winter rainfall will rise by 50mm a month over the next century.
In the UK, analysts at Barclays projected a 3.4% fall in the construction sector for the first quarter of 2012 – attributed in large part to poor weather conditions. And now with a recent study by BRE (Building Research Establishment) also predicting a 6% increase in UK wind speeds, construction output is sure to suffer unless contingencies are put in place.
COMBISAFE UBIX® temporary roof system
The challenge for contractors is simple – stop the weather to stop the delays. But as the severity and duration of weather conditions is so notoriously difficult to predict, contractors look for ways to compensate rather than negate. The most common method is to minimise the delaying effects of weather by protecting a site from the elements. One product that does just this is a temporary roof system, such as the COMBISAFE UBIX® temporary roof system.
For both contractor and client, a carefully considered build programme which takes into account the effects of adverse weather is crucial to every project’s success. However even these are subject to change, and so a temporary roof offers the contractor the additional assurance that the project remains on track.
Traditionally, construction companies forecast periods without precipitation for the completion of critical path project elements, such as the setting of concrete. Now, temporary roofs can keep sites on course and fully prevent rainwater ingress at any time of year. Whether for a short term summer project or extended use in extreme weather conditions such as rain, wind and snow, the UBIX temporary roof meets the challenge.
Flexible and versatile, the UBIX temporary roof can also feature a COMBISAFE RunWay system which means it can quickly and safely roll open to allow for plant, equipment and materials to be craned in and out as required. This system was utilised to provide weather protection at a 12 week archaeological dig at St Bartholomew’s Hospital in London, helping archaeologists to work unaffected by the weather, and in turn allowing vital construction works to continue as soon as possible and keep the £1 billion redevelopment project on schedule.
Without a construction plan in place, or a temporary roof in position, vital construction contracts will continue to be delayed by weather and contractors will feel the impact where it matters most – at their bottom line. Helping projects to stay on schedule no matter what extremities are thrown their way, temporary roofs provide vital protection for workers, machinery, tools and structures to keep projects on time and on budget.
More info @
http://www.combisafe.com