Welcome to ADS Security Installations Ltd, we are a family run company offering a complete site security service. With over 15 years experience in the security industry we have a wealth of knowledge in this industry. We are based in London & Hertfordshire and although the majority of our work is London based we cover anything within a 100 mile radius of London.
As a family run company we pride
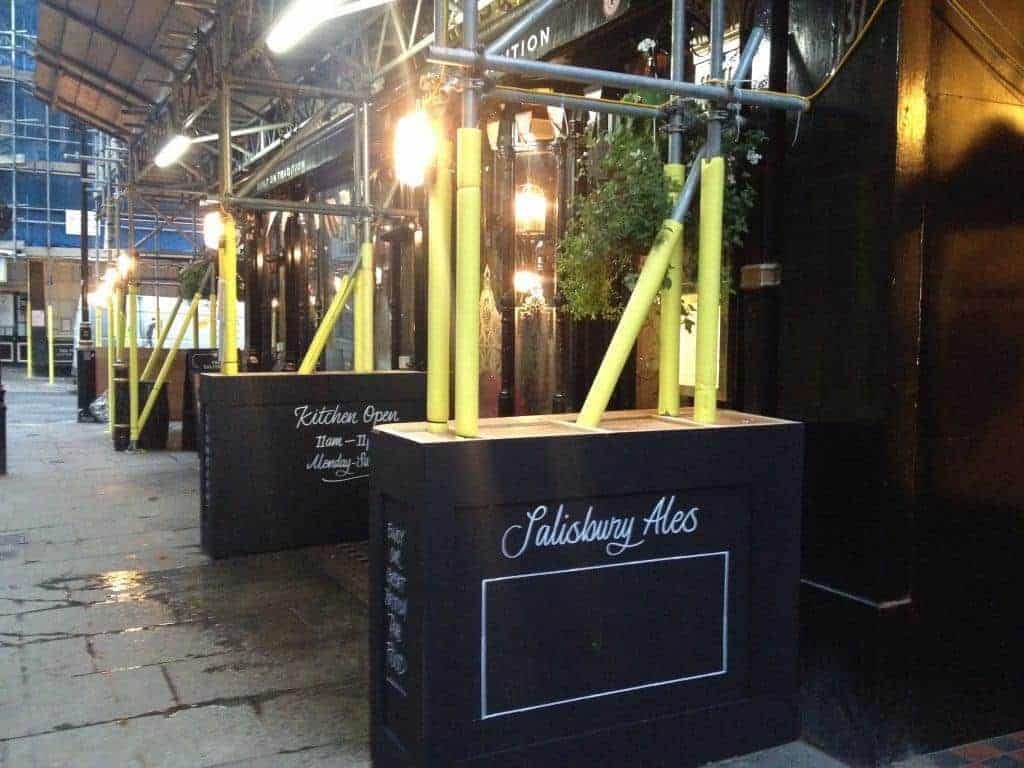
ourselves on the more personal approach, reliability and presentation. We believe presentation is a key factor in our industry as the majority of the time it is our alarms, lighting, hoarding etc that your customer see’s first. With this in mind we take great pride in our work and ensure all our clients are satisfied with our high level of service.
Here at ADS we are constantly innovating new products and offering new ideas relating to the site security industry. As a result we are the only scaffold alarm company to use LCD keypads on all our hardwired installations & all CPU’s are mounted in secure IP rated enclosures. We feel this keeps us steps ahead of our competitor’s which are still currently using analogue alarm systems and mounting them on a piece of wood. We prefer to use the more user friendly equipment, also our alarms look nice and tidy when installed in any home, office, site etc. ADS Security Installations makes it’s own high industry standards and make sure they are adhered too at all times. All equipment is regularly tested and complies with all UK & EU regulations and all installations meet the requirements of approved insurance installations.
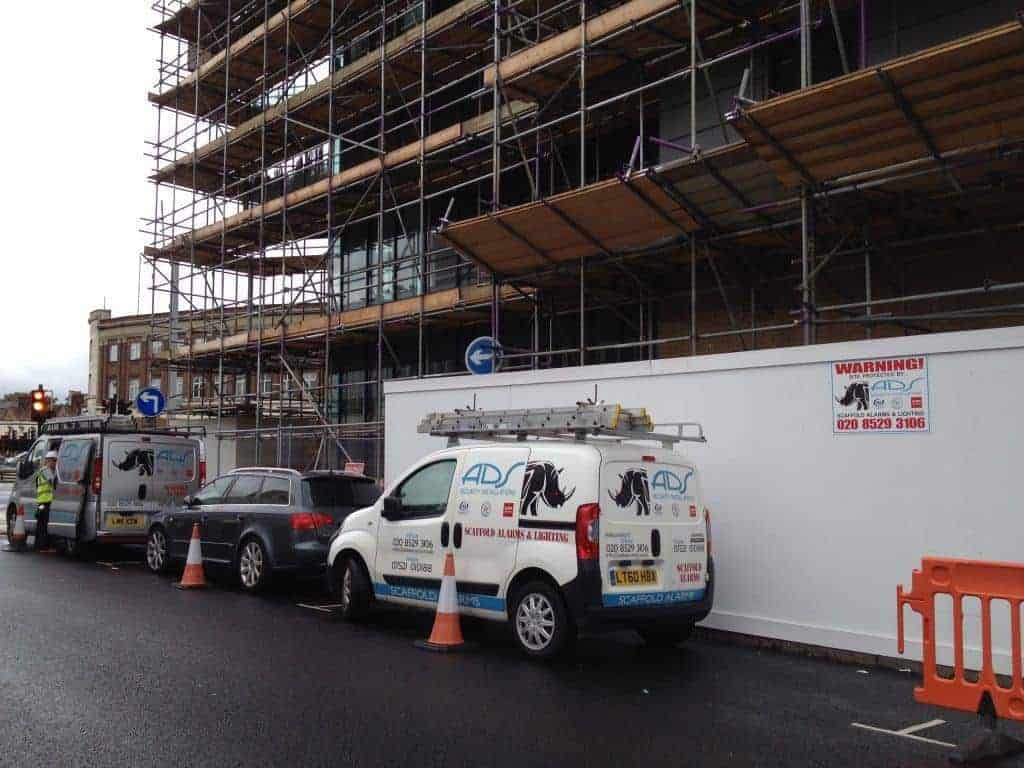
Our business model is to offer our customer’s a professional and reliable service that doesn’t cost the earth. As we offer multiple services we can provide discounted prices on complete site security services, making us a one stop shop for all your site / scaffold security needs!!! We believe in treating all customer’s the same whether it is a small homeowner or a large contracting / scaffold firm. After all a poor installation is as good as no installation at all. We pride ourselves on our quick response, customer satisfaction and knowledge of the scaffold / construction site industry.
Safety is also a key part of our business and a a result of this we are Safe Contractor approved. Also all our operatives are CSCS & ROSPA ( safe working at height ) certified.
Our prices reflect our individuality and we are able to offer huge trade discounts for the larger, longer term contracts. We believe our prices are amongst the best you will see and we are so confident that we will offer a price match guarantee on all scaffold alarms & hoarding in London and surrounding areas.
WE OFFER A 20% DISCOUNT FOR ALL NEW CUSTOMER’S!!!
Please get in touch for your no obligation quotation and remember to look out for the Rhino on a site near you!!!
Contact info:
Website:
www.adssecurity.co.uk
email:
[email protected]
office: 020 8529 3106
mobile: 0752 1010 188
twitter:
@scaffoldalarms
Our services include:
Scaffold / site alarm systems
Scaffold / site lighting ( 110v, 12v, battery operated )
Scaffold / site hoarding ( built to your exact requirements )
Alarm monitoring
Manned response & key holding.
Security fencing ( GS7 ) & Heras fencing.
Temporary electrics ( installed by 17th edition qualified electrician )
Scaffold yard – alarms & CCTV