The UK’s oldest scaffolding contractor, Palmers Scaffolding – formed in 1880 by Edwin Palmer – has a new owner.
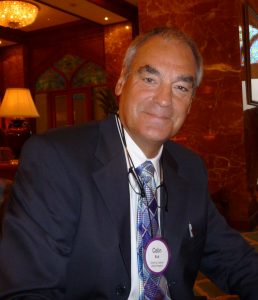
British entrepreneur Colin Butt who runs a number of established business from his UK base at Aviation House, Aviation Park, Chester becomes the new owner.
In a divestment process at the end of 2016 (which came into effect January 4th 2017), the leading scaffolding and access solutions brand Palmers was sold to businessman Colin Butt by previous German owners XERVON GmbH, who were looking to off-set some of their non-EU businesses, post Brexit.
The now British-owned and run Palmers Scaffolding UK Limited business – which employs 300 staff and consistently ranks in the top 10 of UK scaffolding contractors with multi-million pound turnovers (£15.3M 2016) – will continue to run leading scaffolding and access solutions across the UK operationally from its branches strategically located across the country, from Vauxhall in central London to Belvedere in Kent, Bristol in the South West, Chester in the North West Middlesbrough in the North East and up to Glasgow in Central Scotland
As one of the UK scaffold industry‘s leading access, scaffolding and related industrial services providers, Palmers Scaffolding UK Limited will continue to focus on working on some of Britain’s leading projects and most important sites within the construction, airport, railway, petrochemical, power generation, marine and nuclear market sectors.
New owner & Palmers Scaffolding UK Limited CEO, Colin Butt said: “We are thrilled to be the proud new owners of such an historic brand as Palmers – who continue to operate at the highest level of Special Access provision, have a highly skilled workforce. They have established excellent, pre-qualified working relationships with some of the country’s leading contractors and we are looking forward to moving the brand forward in 2017 and beyond and working on some of the biggest, most important projects in Britain in coming years.”
Palmers Scaffolding UK Limited Managing Director, Donald Morrison comments: “It is very exciting times for the Palmers brand. Quality, Health, Safety and Environmental excellence has been, and will remain, the number one priority in the delivery of our business. For over 130 years, Palmers have provided a quality service to all industries. We know that the highest levels of service and performance in our areas of supply can only be achieved through collective involvement, commitment and teamwork. And with Colin Butt’s vast experience in the Special Access sector, his connections, enthusiasm and entrepreneurial skill set, it can only mean greater success for Palmers in the future.”
All Palmers corporate branding and staff remain unchanged with Donald Morrison MD supported by Lindsay Harle Director, Ian McFarlane Director Business & Project Development together with Colin Butt as the new CEO