The Voice of Scaffolding Since 2008 | U.K. Edition
Scaffolder receives life-changing injuries after 9m fall
A bristol based scaffold firm has been fined after a scaffolder was seriously injured after falling nine metres.
Bristol Magistrates Court heard how on 23 July 2013 an employee of Tubular Access Scaffolds Limited was dismantling a scaffold structure when he fell, causing life-changing head injuries. An investigation by the Health and Safety Executive (HSE) into the incident, which occurred at Berkley Crescent, Clifton, found that there was no evidence of preventative measures taken by the company before the incident. Tubular Access Scaffolds Limited, of Duckmoor Road, Ashton, was fined a total of £26,250, after pleading guilty to offences under the Work at Height Regulations 2005. Speaking after the hearing Health and Safety Executive principal inspector Helena Tinton said: “If the company had managed a safe system of work with properly trained and equipped scaffolders, then the employee would not have suffered such terrible injuries.”Video: Scaffolding Training in 1969
A video has emerged showing how scaffolders were being trained in 1969.
British pathe has published a very interesting snapshot video of scaffolders being trained at the old CITB scaffold training center in Mitchem, London. Well before harnesses and the conception of SG4 & TG20, the video profoundly highlights how far our great industry has progressed to become a world leader in scaffolding training and safety. The video also shows Big Ben and parts of Westminster covered in scaffolding. Old school scaffolders, we salut you. Let us know your thoughts in the comments below.SG4:15 – Preventing falls in Scaffolding Operations announced
The NASC have announced the latest edition of the safety guidance SG4 – Preventing falls in Scaffolding Operations.
For almost 20 years and 200,000 copies later the popular guidance notes SG4 continues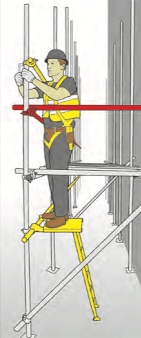
TRAD Group – Going for Growth
New TRAD Commercial Vehicle Fleet – Protecting People and the Environment and enhancing service levels.
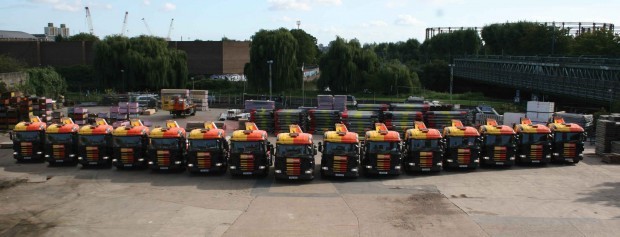
TRAD is proud to announce the completed purchase of 15 new Scania HGV units complete with 1.5 Ton Fassi Cranes at a cost of £1.7 million. These modern high quality vehicles are fully Euro 6 compliant helping us to protect the environment by reducing emissions, particularly in London where TRAD Co mainly operates, this is part of our continuous drive to reduce our carbon footprint and improve our Environmental Management System accredited through BSI to ISO 14001.
Moreover, as part of our continuing focus on improving safety for our Employees and the General Public, all 15 vehicles have been fitted with top of the range cameras. These enhancements help protect Cyclists and Pedestrians by substantially reducing blind spots in the Driver’s field of sight. TRAD currently holds Bronze FORS Accreditation and this purchase of the new Scania HGV units solidifies our commitment to achieving the FORS Silver standard early next year.
Furthermore, these new Lorry Loader Cranes enable a much safer working environment with a major advancement in remote controlled Lifting Operations. All TRAD’s HGV drivers have received certificated Training, allowing them to control every aspect of the lifting process from any position around the truck, thus resulting in increased visibility of all operations improving safety and enabling us to give a better quality service to our customers.
New Trucks – New Livery
The new trucks have been liveried with distinctive new paintwork and visuals, helping them to stand out and promote the TRAD and ALTRAD brands. Featuring striking graphics and the ground-breaking use of “chrome” film, the vehicles promote our new ‘Metrix’ scaffolding system, as well as the five key safety behaviours that form our Behavioural Management of Safety Programme, Play it Safe. They also celebrate our parent company the ALTRAD Groups affiliation with the Montpelier Rugby Club, which is personally owned by Mohed Altrad.
The trucks have been transformed into a highly effective form of mobile messaging, promoting continual awareness of our Behavioral Management Programme ‘Play it Safe’ as well as promoting both the TRAD Group and ALTRAD Group Brands.
NASC shortlisted for Pride of Construction Award
The National Access and Scaffolding Confederation (NASC), has been shortlisted for a top award for its outstanding commitment to supporting apprentices.
NASC is in the running for a prestigious Pride of Construction Award at the annual industry prize-giving run by the Construction Industry Training Board (CITB). The awards celebrate all of the best people, companies and partners in the construction industry. This year’s ceremony, which takes place on 25 November at the Natural History Museum in London, arrives at an exciting time for the construction industry, with 10,000 jobs forecast to be created in Greater London alone over the next five years. The NASC has been nominated in the Outstanding Strategic Partner category in recognition of its best practice initiatives such as its commitment to apprenticeships, and its promotion of the scaffolding industry training scheme (CISRS). NASC Director of Training, Dave Mosley commented: “We are very pleased to be nominated and shortlisted for this Pride of Construction award. As the UK’s scaffolding and access trade body (NASC) we work closely with CITB to make the construction industry a safer place in which to work. “It’s gratifying to receive recognition from CITB for our role in achieving this; and indeed to be recognised for our work as a CITB strategic partner. We have a long and proud history of working with CITB, helping to raise the profile of industry training in the construction sector.”Workers jump for their lives as scaffold collapses
Three firms have been prosecuted by the HSE after workers had to literally jump for their lives when a huge scaffold collapsed into the River Brain in Essex.
Renovation work was underway at the Former Riverside Centre, Braintree when on the 1 July 2014 a forty meter run of independent five lifts high collapsed. Workers leapt through open windows to avoid falling with the huge scaffold. The HSE commenced a full investigation into the incident and charged three firms with various breaches of law. Principal contractor Parkland Developments Ltd, scaffolding contractor SC Cousins Scaffolding Ltd and CDM co-ordinator Haze and Safety Ltd all found themselves before Chelmsford Magistrates’ Court. The court heard HSE’s investigation found numerous failings on site;- The CDM co-ordinator had failed to provide suitable and sufficient advice to the client (Parkland Developments Ltd) or ensure that the arrangements were being implemented on site.
- The principal contractor (Parkland Developments Ltd) failed to implement the construction phase plan or ensure that they planned and managed or monitored the scaffolding works.
- The scaffolding contractor failed to plan the work or design the scaffold. They also failed to send trained and competent workers to site. In the weeks prior to the collapse, a scaffolding labourer was acting as the supervisor and overseeing trainee scaffolders in erecting, altering and inspecting the scaffold.
- Not one of the duty holders had identified there was no design for the scaffold.