The Voice of Scaffolding Since 2008 | U.K. Edition
TRAD Scaffolding Celebrate Successful Client Seminar
Following recent changes to scaffolding safety standards, TRAD Scaffolding invited its clients to attend a seminar on Thursday 14th April 2016 in St Paul’s, London.
Pushing Boundaries – SG4:15 & Beyond outlined how TRAD Scaffolding intends to approach the new standards, which address the prevention of falls in scaffolding operations.
The seminar proudly featured a guest presentation from leading industry consultant Rick Statham, who is also Joint Managing Director at Safety & Access Ltd. Rick discussed the newly updated flagship guidance and how this will affect the industry in practical terms. Described by the UK scaffolding industry trade body as ‘evolution not revolution’, the new SG4:15 standards reflect the increase in TG20 compliant scaffolds and address changes to scaffolding best practice.
The event was hosted by TRAD Scaffolding Managing Director, Neil Garner, who explained the current structure of TRAD Scaffolding. He also showcased the organisation’s leading products, the Plettac METRIX Scaffold System and the Altrix Temporary Roofing System.
There was also a presentation by Des Moore, TRAD Group Managing Director & NASC Vice President. Des spoke about the TRAD Group as well as the complementary products and services that TRAD Safety Systems has to offer. Also in attendance was Hayden Smith, Group Chairman and founder of TRAD.
Speaking after the event, Neil Garner said: ‘I’m really pleased with the high turnout we’ve received. I’ve spoken to a lot of our clients today and they’ve all said that they found the presentation really useful and insightful. As a company, TRAD Scaffolding is always pushing the boundaries of innovation and that’s why we named the seminar ‘‘Pushing Boundaries – SG4:15 & Beyond’’. We want to demonstrate to our clients that TRAD Scaffolding will not only meet these new standards but seek to exceed them wherever possible.’
Steve Clarke, Contracts Director at Coniston commented: ‘TRAD Scaffolding are without doubt the most professional scaffolding company that I’ve dealt with. Today’s event has been a real eye opener, in particular the breadth of design and R&D that TRAD are involved in – especially with Plettac METRIX System Scaffold.’
Heroic scaffolders rescue young woman from car blaze horror
Quick-thinking scaffolders sprinted down from the A1(M)’s hard shoulder and helped a young woman from her wrecked car, just moments before it went up in flames.
Scaffolder Craig Dean, from Letchworth, stepped in to help a young gym teacher Chloë Ward last Friday morning after a motorway shunt sent her car crashing through a fence and into some trees. She ended up needing plastic surgery to her face and lip, and has back and neck pain, but is already out of hospital – and hero Craig paid her a visit on Sunday. “I can’t thank him enough for saving her,” said Chloë’s mum Lisa. “He doesn’t think he is a hero, but he is mine.” Thankful dad Ian agreed: “Craig was the hero of the hour.” Chloë, 22, was on her way to work in Luton, and had only taken the A1(M) in the first place because she was early and fancied a change. Ian said: “We’ve got camera footage showing a grey vehicle veering into her lane, and you can see her being knocked off the motorway. “She went straight into a wooden fence, through an embankment and into the trees.” Craig was driving down the motorway on his way to a job in Stevenage when he saw what had happened. “Me and two of the lads were driving from the yard to work just like every morning,” he said. “Going past I saw the red Vauxhall and a girl down there. “I pulled up and sprinted down with my mate Gerry. She was leaning against the driver’s side of the car, bloodied all over her face. She’d climbed out the window. “I could see flames coming out of the engine so I wanted to get her away from the car as fast as I could. “As we got back to the hard shoulder, it just went up.” Craig and his workmates from First Choice Scaffolding, Gerry Fuller and Neil Stewart, stayed with Chloë while they waited for help to come, as did another passer-by Craig could identify only as ‘Cod’. Neil called an ambulance and Gerry helped to comfort Chloë. Chloë was discharged from hospital the same day, but returned for plastic surgery on Monday. The Ward family is appealing for the public’s help tracing the grey saloon car involved in the collision. Ian said: “He parked underneath a sign and had a look, then drove off.” In particular they are looking for the driver of a white van that was on the hard shoulder behind where the grey car stopped. Police yesterday appealed for the grey car’s driver to come forward. Anyone with information should call PC Philip Watts on 101, quoting ISR 67 of April 29, or Crimestoppers anonymously on 0800 555 111. Via: www.whtimes.co.ukScaffold company fined for safety failings
A Scaffold company in Bridgend has been fined for safety failings following a routine inspection.
Llanelli Magistrates’ Court heard how OW Scaffolding was working at Heol y Parc, Cefneithin when they had a routine inspection which highlighted several safety failings. An investigation by the Health and Safety Executive (HSE) into the incident which occurred on 30 September 2015 found that there was poor planning, inadequate risk assessments, inadequate site supervision and inadequate and insufficient equipment. OW Scaffolding Limited, of Village Farm Industrial Estate, Pyle, Bridgend, pleaded not guilty to breaching Regulation 4 of the Work at Height Regulation 2005 but was tried in its absence and found guilty and fined £1,000 and ordered to pay costs of £3,700.Bilfinger appoints new Operations Director
Bilfinger Industrial Services UK Ltd has announced the appointment of a new Operations Director.
Paul Norton has joined the company as Operations Director, Prior to joining Bilfinger Paul spent the last two and a half years as a Director of a project portfolio management consultancy assisting EDF Energy in managing their capital portfolio across their coal generating assets. With managerial experience over a period of more than twenty years in the UK petrochemical and power sectors, Paul has worked his way from a trade level, through front line supervision to middle and senior management. Over his career Paul has demonstrated his ability in the consistent delivery of results, building high performing teams. He holds a Master of Science degree in Project Management along with a Post Graduate Diploma in Management and is a full member of the Association for Project Management, the Association of Cost Engineers and AACE International. Paul will be based in Axis House, Runcorn but will spend much of his time on our client and operating sites.Betchworth Firm Refused Permission To Run HGV’S
Licence bid turned down after scaffolder shows “insufficient respect” for law
A Betchworth scaffolder who had “insufficient respect” for the law on the operation of vehicles has been refused permission to run HGVs. London and South East Traffic Commissioner, Nick Denton, said he could not trust Daniel Lippett to run a compliant operation. The regulator’s decision to refuse Mr Lippett’s two vehicle application comes after a public inquiry on 23 March. During the hearing, the Traffic Commissioner was told that Mr Lippett had previously served as a director of M & L Elite Scaffolding Services Ltd, which held a valid operator’s licence. As part of his new application, Mr Lippett had indicated the limited company licence would be surrendered. However, Companies House records revealed that he had resigned from the company seven days before the application form had been completed. He therefore had no authority to surrender the existing licence. Mr Denton also heard that the existing licence had an adverse compliance record, with DVSA reporting: · The use of a vehicle without a valid MOT (for over two months and a further month after being stopped by DVSA examiners); · A vehicle stopped displaying a licence disc associated with a different vehicle registration mark. · The use of an unauthorised operating centre (since around October 2014) In his application for a licence in his name, Mr Lippett declared that he was already operating under the authority of the existing licence held by M & L Elite Scaffolding Services Ltd, even though he had left that company. Giving evidence to the Traffic Commissioner, Mr Lippett said at the time of the DVSA stop in October 2015, he thought the vehicle had an MOT certificate. On purchasing the vehicle in February 2015, he was assured that it had 12 months MOT. Mr Lippett subsequently accepted that he had not checked this or seen the certificate confirming the MOT. The Traffic Commissioner asked Mr Lippett why he had continued to operate the vehicle after the stop for a further month, knowing it did not have an MOT. Mr Lippett explained that, having made a booking for the MOT, he thought it was legal to continue operating. Responding to a question on the availability of safety inspection records, Mr Lippett told the Traffic Commissioner they had been retained by a DVSA traffic examiner. Mr Denton adjourned proceedings to allow these records to be produced and told Mr Lippett that if there was any chance of him being considered fit to hold a licence, his vehicle should not be operated in the meantime and that he should attend an operator licence management course. In written correspondence to the Traffic Commissioner, Mr Lippett subsequently accepted that he had made an error in saying DVSA had retained his safety inspection records. He produced four PMI sheets, which showed the six weekly inspection frequency had been exceeded. He had also attended an operator licence management course and provided photographic evidence of the vehicle’s odometer reading. That evidence revealed the vehicle had travelled 152km between 24 and 30 March 2016. Mr Lippett claimed a driver had taken the vehicle in error but the Traffic Commissioner said if he had been truly serious about ensuring it was not used, he would have taken effective steps to prevent it from happening – such as keeping the keys. In a written decision, Mr Denton said: “I find that Mr Lippett has insufficient respect for the law on the operation of vehicles, as instanced also by his continuing to use a vehicle in an unroadworthy condition for a further month after the DVSA stop had told him beyond all doubt that the vehicle had no MOT.”New CEO at Actavo Industrial Division
New senior appointment at Actavo
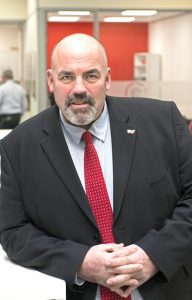
PASMA launches new advanced training course
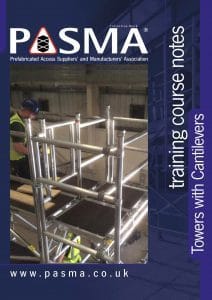
Dramatic video captures collapse of scaffolding from highrise building
Onlookers capture shocking footage of scaffolding collapsing from a nine story building in Japan during high winds.
Video has emerged online of the moment when high winds peeled away scaffolding and metal panels from a nine-story building that was due for demolition in Tama, western Tokyo, Japan. The incident happened on Sunday (17 April) thankfully there has been no reports of any injures. Let us know your thoughts in the comments below.Vice Chairman of PASMA retires from Council
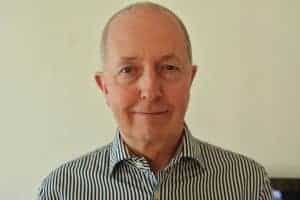