The Voice of Scaffolding Since 2008 | U.K. Edition
Trainee Scaffolder Falls To Death At Sydney Construction Site
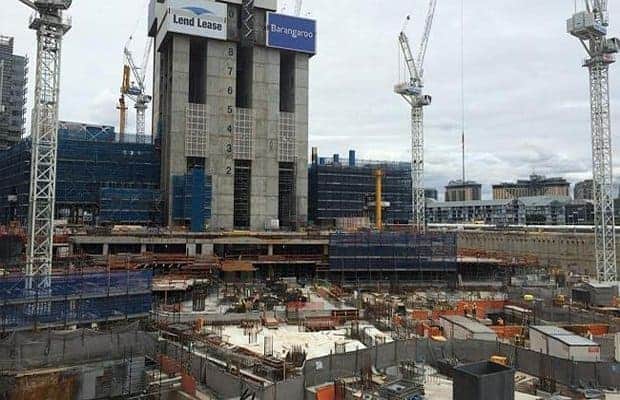
Trainee Scaffolder plunges to his death after 30 meter fall in Barangaroo near Sydney Harbour, Australia.
The trainee scaffolder in his 30’s fell from scaffolding on the construction site after only being on the job for two weeks reports say. The man had been on the Koori Job Ready Programme, which helps train up young aboriginal people for the construction industry. Emergency services were called to the site at about 8:30am (AEDT) The Ambulance Service says the man’s colleagues performed CPR until they arrived. Paramedics pronounced him dead a short time later. Police are investigating the possibility the scaffolder had suffered a medical problem before he fell. Reports also suggest there is inadequate supervision at the Lend Lease Barangaroo construction site. Union officials said about 500 workers had stopped work because of the accident. They would meet again on Friday morning before deciding if they would return this week. Barangaroo is the site of a controversial waterfront development on Sydney Harbour which will include commercial offices, apartment buildings and a casino.Safety Alert Issued On Defective Scaffold Boards In Northern Ireland
Northern Ireland’s Health & Safety Executive (HSENI) have issued a Safety Alert.
Broken scaffold boards have recently caused an increase in serious accidents on construction sites in Northern Ireland. The majority of injuries happen when boards used in ‘platform brackets’ break during normal work activities. HSENI find during their site visits that there are boards in use which superficially look sound, but on closer inspection are found to have been weakened. It is vital that you have a system of work which ensures that all scaffold boards are checked regularly for damage, rot or any other feature which may reduce the strength of the board. The misuse of boards can cause serious damage. Do not use scaffold boards to:- assist vehicles over soft ground
- store heavy objects, for example, lifting pallets of blocks on to scaffolding at areas which are not specifically designed loading bays
- make a ramp for wheel barrow access
- driving vehicles over boards unintentionally
- throwing or dropping boards from heights
- impact loads, for example dropping heavy sills
- fungal decay, for example wet rot
- broken or damaged end bands
- wood broken from the edge of the boards which significantly reduces the cross-section of the board, for example, notches
- loose or broken knots
- excessive cuts in the faces of boards caused by hand saws, circular saws or angle grinders (trades likely to use power tools on scaffold must use sacrificial timber and not cut directly onto scaffold boards)
- transverse cracks caused by overloading.
- infestation of the timber, for example, holes caused by insects
Storage of scaffold boards
Decay in your boards can be reduced by storing planks properly when not in use. This is particularly relevant in these economic times when large quantities of scaffolding may be stored for longer periods of time. Boards should be stored preferably under cover and clear of the ground. Spacers must be used between each layer of stacked boards to allow an adequate flow of air around the boards to dry them out. To prevent further accidents check to see if the scaffold boards you are using comply with the following:- all scaffolding boards conform to BS 2482:2009
- they are cleaned prior to inspection – all surface contamination which obscures the surface of the board, for example, cement must be removed before inspection – this can usually be done using a paint scraper or a stiff hand brush
- boards are inspected prior to being put into use, at regular intervals whilst in use and before storage
- they are not damaged beyond the limits in the British Standard including cracks, cuts or notches cut out of them
- damaged / defective boards are immediately taken out of use and disposed of appropriately
- all boards in storage are stacked in a way which allows for ventilation
- where machine testing is carried out ensure that boards are tested in both directions
Stork Technical Services Sells Its Subsea Division To N-Sea Group
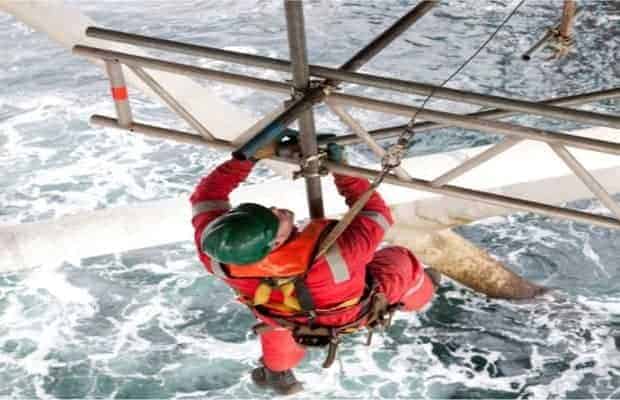
A Responsible Payment Culture – The Government Wants SME’s Input.
Article written by Colin Hale
A most interesting Discussion Paper found its way into my email inbox the other day. Entitled “Building a Responsible Payment Culture”, it has been prepared by the Department for Business Innovation & Skills (BIS), with a forward written by Vince Cable (Secretary of State for Business, Innovation and Skills). I opened it with all my usual scepticism and settled down for a read through the same glib aspirational stuff that repeatedly gets hauled out in documents such as this. I was however pleasantly surprised by its meaningful content and felt moved enough to write this article. The paper is essentially a consultation document and canvasses views on payment culture, both as it stands at the moment and what could be done to improve it. It is not limited to construction, but that said I feel that the construction industry bears the brunt of payment abuse and Specialist contractors could provide the most positive impact. Specialist contractors, through bitter experience, know only too well how they are affected by the often irresponsible payment culture of main contractors and their propensity to bank with the ‘Bank of Sub-Contractor’ for longer than is either morally defensible or contractually correct. How to address this imbalance is something that has been wrestled with in the construction industry for decades without real improvement and main contractors simply pay lip-service to any payment responsibility code or charter and continue misusing the ‘purchasing power’ they enjoy, in most of the normal commercial circumstances. The Government appears to finally have recognised the severe, and entirely unnecessary, administrative and financial burden put on small to medium businesses every year simply because such businesses are not paid properly. It has determined that the impact of late payment stops businesses from investing to grow, creating new jobs, paying their suppliers properly and from contributing fully to economic prosperity. Not exactly a rocket-science conclusion but at least it is something on which to build. The consultation that the document seeks to draw upon is what Government, businesses and other stakeholders can do (collectively and individually) to build an environment where larger businesses treat their suppliers fairly and accept their obligation to pay what they owe, when they owe it and, if possible, without over-burdensome and complex enforcement legislation The paper seeks views on-
whether more can be done to change business culture through measures to enhance accountability and transparency;
-
how to encourage small businesses to make better use of the statutory rights they already have and whether there is a case to enhance those rights; and
-
how the Government can help small businesses to help themselves to reduce the risk of late payment
-
“If you are being paid by either by the Government or any private Employer at anywhere between 14 to 28 days from the end of the month, why do you need 60+ days from the end of the month to discharge payment to the Specialist?”
-
“What do you do with the money that you have received in the period between the date that you get paid (14 to 28 days) and the date that you release payment (60+ days)?”
-
to issue sub-contract terms that filter down from the Main Form of Contract (which will often be a standard JCT or NEC version) with an equivalent JCT or NEC Sub-Contract;
-
to ban hybrid sub-contracts in their entirety. These are often so onerous and written simply to give the main contractor a further unfair advantage (not content with sitting on monies for inordinate amounts of time, it wants to impose as many unfair conditions as possible to stop the Specialist getting paid). Such unfair advantage was not the intention of the standard Contract forms;
-
to pay Tier 2 Specialist contractors within 30 days (this can work providing Government / Private Employers pay main contractors within 14 to 28 days, which most do, of the Valuation dates);
-
to introduce a requirement that the first payment to the Specialist is to be certified no later than 30 days from commencement of the Specialist’s commencement on site;
-
to ensure that ALL construction contracts over a certain size (for example, £100,000) are administered via a Project Bank Account (effectively ring-fencing the monies) and that this Project Bank Account used for the benefit of the Specialist contractor;
-
to ensure that the main contractor passes on to the Specialist the benefit of any Advance Payment that it receives, or alternatively to ensure that ALL contracts have provisions for an Advance Payment;
-
that interest for late-payment is punitive (say 15% plus over base) and certainly not less than the current rate of interest payable by the Late Payment of Commercial Debts (Interest) Act 1998. All too often the main contractor changes the contractual interest in respect of late payment to 2% or less above base (making it then a cheap method of borrowing).
For further information please contact Colin Hale by email on [email protected]
The paper “Building a Responsible Culture” can be downloaded from www.gov.uk\government\consultations/late-payment-of-finance-building-a-responsible-payment-culture or can be requested by email to [email protected]
Hampshire Scaffolding Firm Secures Loan To Grow
A Scaffolding firm based in Hampshire has been able to expand after securing a Government-backed loan.
Jarrett Scaffolding has secured a £50,000 discounted rate loan through NatWest as part of the Government’s Funding for Lending scheme. The scaffolding firm was set up by Jay Pinnells who wanted to grow the company by taking on bigger contracts and stocking up on more materials, the Government-backed loan has also enabled him to add another heavy goods vehicle to his fleet and three new scaffolders. Mr Pinnells was recommended to the bank by his accountant Daleep Pandey and was assisted by Annie Cains at the NatWest Southampton office Mr Pinnells said:“Without NatWest we wouldn’t have been able to expand”. “Annie was absolutely fantastic; she is highly professional and methodically helped us through every step of the loan application. “Annie is a pleasure to work with and as our business manager she continues to be on hand to offer advice and help with any queries.” Annie added: “I’m so pleased we’ve been able to support Jay and his business, helping him towards his business ambitions. I’m looking forward to working with him to help him continue the success of his business.”
48.3 Scaffold Design launches new website!
The 48.3 Scaffold Design team are delighted to unveil their new look website.
Since 48.3 Scaffold Design started trading three and half years ago, their image and logo has evolved. The orange branding has always featured in their website even from the start, and now not only does their new website look clean and striking with its bold white headlines on dark blue imagery but still features the 48.3 Scaffold Design corporate ‘Orange’ ensuring they don’t forget their roots! Ben Beaumont, Founder and Managing Director at 48.3 Scaffold Design told ScaffMag:The details are:“The new expanded website reflects the growth 48.3 have achieved over the last 12 months particularly. We really wanted our reputation for quality and service to be reflected in our website, and we feel the new design does this perfectly. Our design team will grow to six in January 2014, and all our members will be fully competent design engineers or technical design draughtsmen.
We strive to be the best and pride ourselves on offering an innovative tailor made service to our clients. We offer a dedicated team who provide a fast and efficient turnaround on projects, delivering cost effective and efficient solutions. The website has allowed us to showcase our design service and highlight the details that set 48.3 apart from our competition”.
-
Their clients enjoy a design turnaround of 5-7 working days, guaranteed no greater than 10 working days!
-
They meet agreed deadlines, if they don’t they will do the design for FREE!
-
They can save you up to £1250 a month! – with there sliding scale of design fees, mean the more work they do for you, the more you will save.
-
They provide a ‘Fast Track’ scaffolding design service for time critical projects ensuring a guaranteed start within 24 hours!
The new website incorporates a new ‘About Us’ page where you can meet the team and read about the 48.3 Mission, Vision and Values which provide the driving motivation to the delivery of our design service”.
These days everyone is ‘on the go’ and it was important for them to make sure the website was responsive, this means whether you are viewing them on your Mac, laptop or mobile, the pages of the website can adapt to suit the size of your screen. In addition their portfolio pages and news pages have been completely redesigned allowing them to showcase their designs and news in the best and most effective way, plus they have an interactive ‘Contact us’ page featuring a grab and drop map as well as a link to their Google + page. In addition all their social media sites such as Facebook, LinkedIn and Twitter (@483ScaffDesign) have been rebranded too! Visit their new website at www.483scaffolddesign.comVIDEO: Northamptonshire firm fined after scaffold collapse
Northamptonshire shoppers were forced to run for safety as a scaffold collapsed and fell some 20 metres towards them, a court has heard.
Nobody was hurt, but several people required treatment for shock as a result of the incident at the Willow Place Shopping Centre in Queen’s Square, Corby on 17 August 2012. Local firm Desborough Scaffolding Limited, of Desborough, was prosecuted today (16 December) by the Health and Safety Executive (HSE) after an investigation established that the scaffold was structurally unsound. Northampton Magistrates’ Court was told that debris netting had been fitted to the scaffolding tubes, but in high winds on the day it acted as a sail and caused the structure to pull away and apart – sending metal poles and other materials raining to the ground below. The falling scaffold smashed through shop canopies below and also pulled down signs. Several businesses were forced to close while the clean-up took place and the area was made safe. The incident was captured on CCTV. The HSE investigation found the scaffold had not been erected in a way to ensure it would remain stable, and had not been designed by a competent person to ensure it had adequate strength and rigidity for the purpose and environment it was to be used in. Desborough Scaffolding Limited, of Stoke Albany Road, Desborough, were fined £16,000 and ordered to pay £4,678 in costs after pleading guilty to single breaches of the Work at Height Regulations 2005 and the Construction (Design and Management) Regulations 2007. Speaking after the hearing, HSE Inspector Sam Russell said:“It was sheer luck that no-one was seriously injured or killed as a result of this totally preventable incident. “Scaffolding erected to an approved design by competent persons should be able to withstand high wind loads without failing. “This case highlights the requirement of following prescribed industry designs and manufacturers’ instructions. The company’s failure to do so put innocent workers and members of the public at significant risk.”News Source: HSE
John Brash becomes only UK Company to receive Benchmark accreditation for fire treatment Scaffold Boards.
There are no second chances with scaffold boards; whether it is grading them during manufacture or fire treating after it’s vital that the specification is both correct and adhered to. The consequences of failure are serious either to health or safety. There is a greater awareness for the use of fire treated timber scaffold boards. There are invariably used offshore within the North Sea Oil and Gas industries, with London Underground and increasingly within construction.
John Brash takes this risk seriously; for many years its scaffold boards have carried the kitemark symbol of quality with licence number and dual graded to ensure board performance.
Christian Brash comments:
For further information on JB Firesafe specifications and the fire retardant treatment of scaffold boards read the technical article.“All manufacturing has always been carried out within our ISO 9001 system. To ensure the highest standards are consistently met the WPA (Wood Preserving Association) has developed its Benchmark accreditation for timber treatments. John Brash has been the first to be awarded this for the fire retardant treatment of scaffold boards.
“This is an important certification for us. We’ve heavily invested in our treatment plant to deliver a quality service within exceptional lead times to our customers. The WPA benchmark scheme is important to anyone buying treated timber to ensure the product is fit for purpose. WPA benchmark, in conjunction with the kitemark scheme for grading, ensures total peace of mind for the client. This sits very nicely alongside our approvals for use within London Underground where we have demonstrated we meet all their quality and identification requirements. ”