The Voice of Scaffolding Since 2008 | U.K. Edition
Avontus Case Study: Niles Plant Services LLC
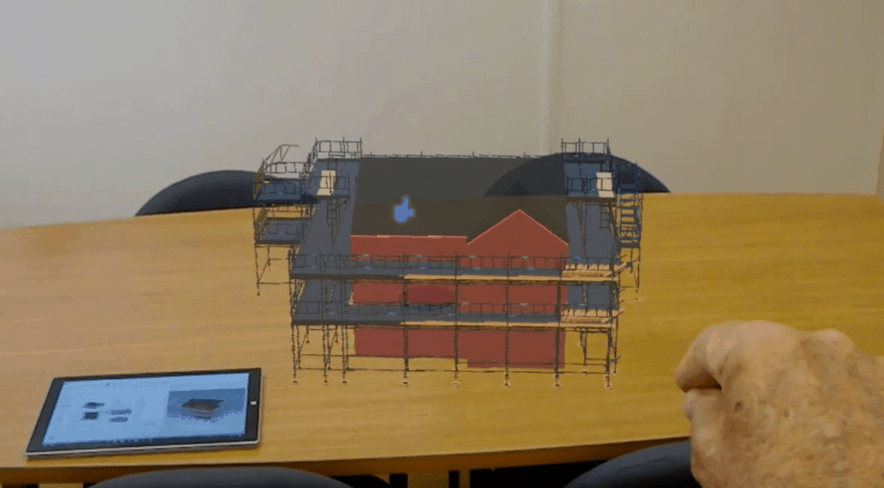
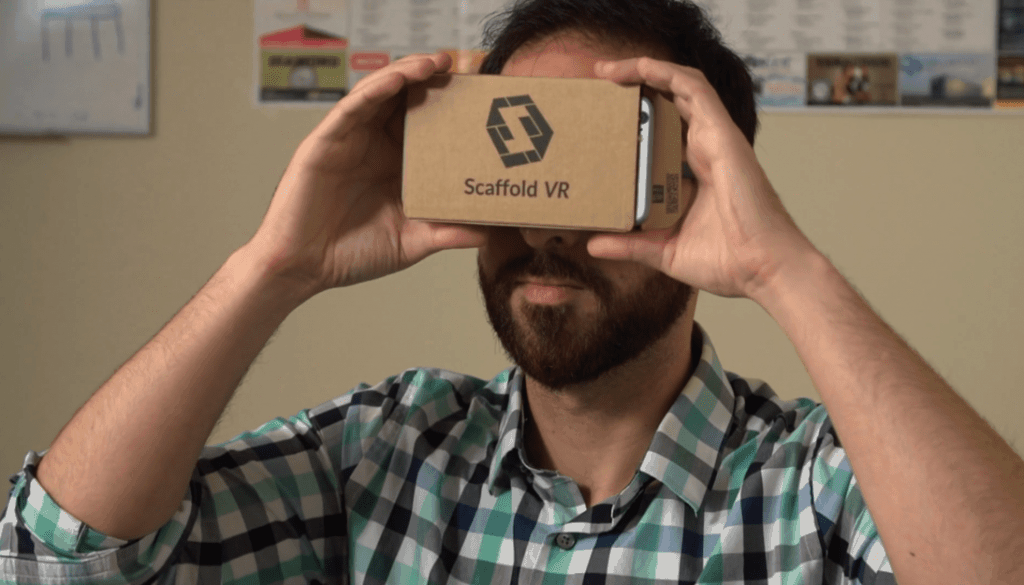
Palmers Provide Innovative Scaffolding Solutions at Carlisle Rail Station
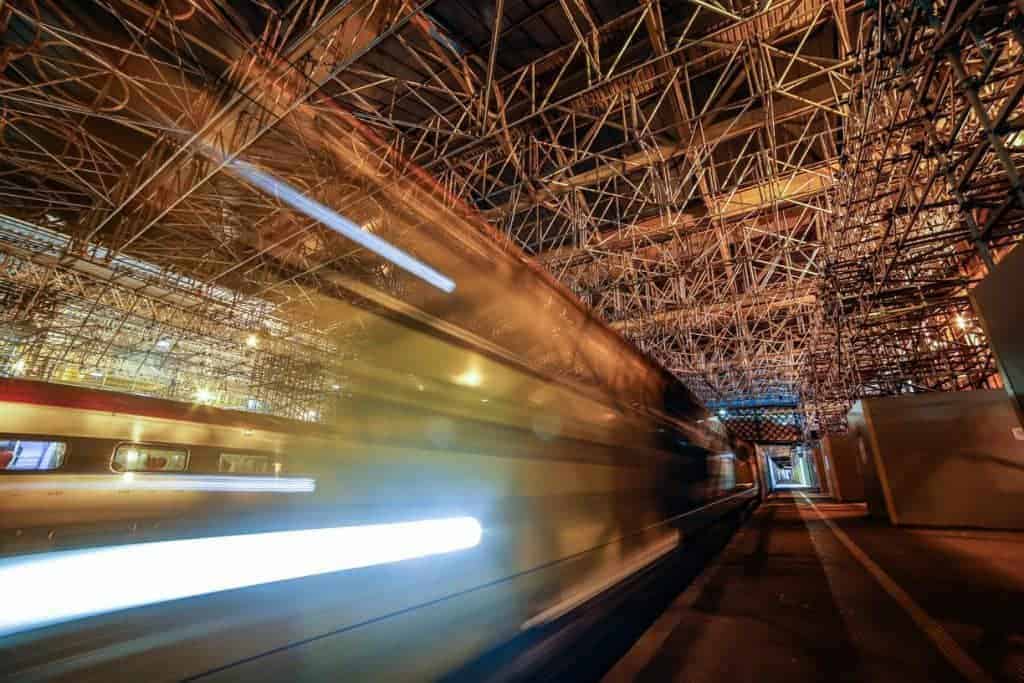
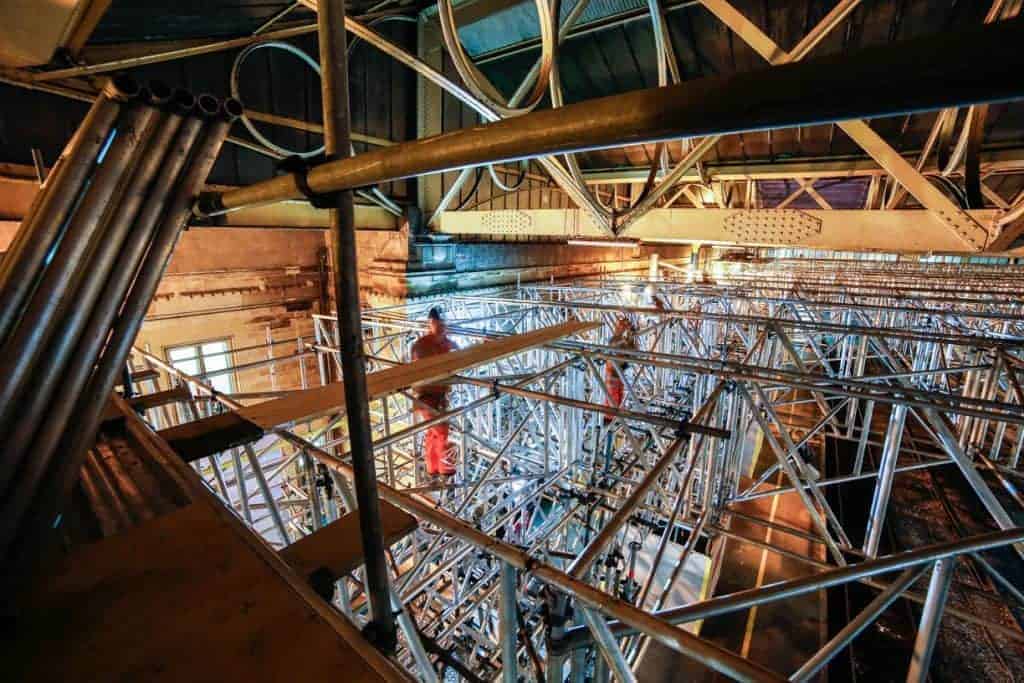
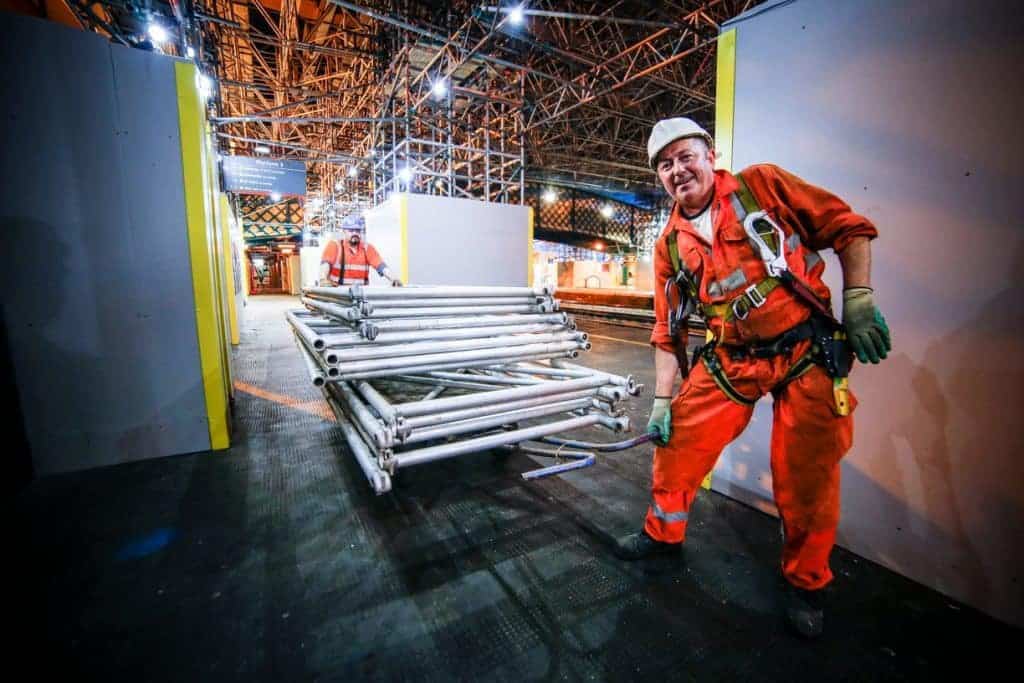
Mercer Scaffolding aims high with new Mercedes-Benz trucks
Mercer Scaffolding has continued to raise its ambitions by investing in three state of the art Mercedes-Benz trucks.
They include a 15-tonne Atego 1518, and two 26-tonne Arocs 2530 models with factory-fitted four-man benches behind the two front seats. This enables each to carry a driver and a crew of five scaffolders in safety and comfort. These new trucks are fitted with specialist dropside flat-bed bodies, used to carry scaffolding equipment such as tubes, boards and fittings. All three vehicles have Classic-space cabs – L-cab versions for the two Arocs, an S-Cab for the Atego, finished in bright orange. These feature the Mercer logo alongside that of Help for Heroes – the operator is an enthusiastic backer of the charity, supporting servicemen and women injured in the line of duty. As a family company they are based at Longfield in Kent, overseeing ongoing projects in both London and the South-East. The firm takes pride in offering its clients competitively priced, ‘all-in-one’ scaffolding solutions. Solid in construction the impressive Mercedes-Benz Arocs range of rigid trucks from 18-32 tonnes GVW and tractor units, are purpose-designed for construction-related applications. An advanced Atego, flies the flag for the three-pointed star in the 6.5-16 tonnes GVW segment. A popular choice for operators in the construction and associated sectors, most are used for light- and medium-duty distribution work. As a forward thinking business Mercer has introduced new management systems and procedures, as well setting up its own transport operation to service larger projects. It achieved Bronze accreditation from the Fleet Operator Recognition Scheme (FORS) last year, and sees the new vehicles as vital to securing Silver status towards the end of 2017.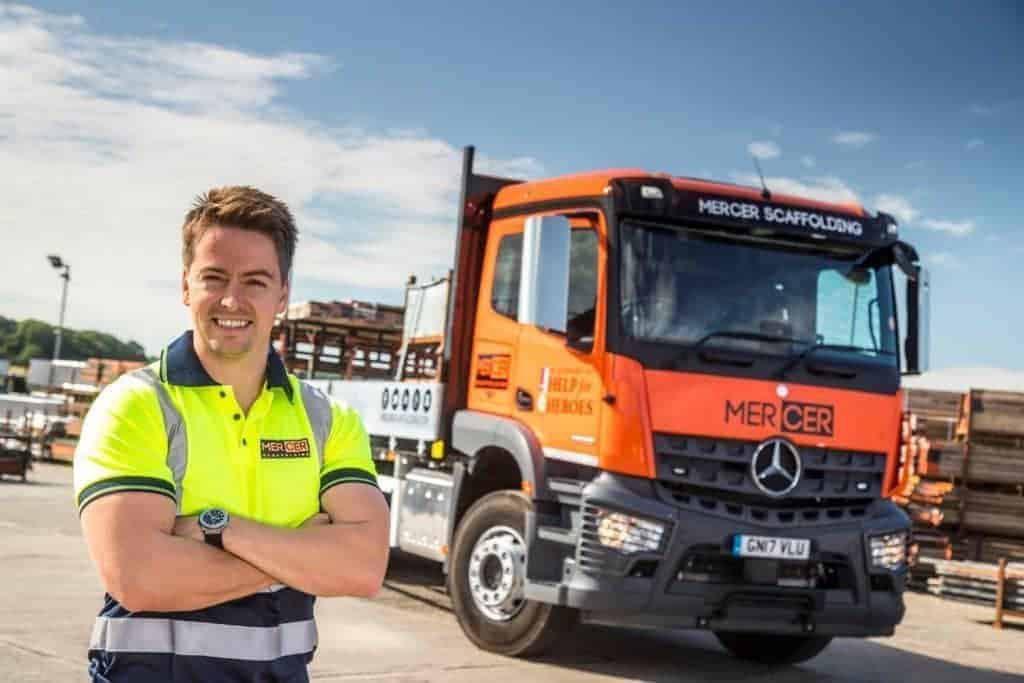
Scaffold firm fined 27K after untrained worker falls
A scaffolding company has been fined after a worker was left in a coma after falling from scaffolding.
Safety & Access to Hold Networking Event
Industry Stunned After Death of Safelinx Inventor
Industry in shock after news of well known industry pioneer and inventor dies suddenly
Its with great sadness I have to inform our readers of the sudden death of well know industry pioneer Nick Flynn who passed away from a heart condition late Tuesday afternoon.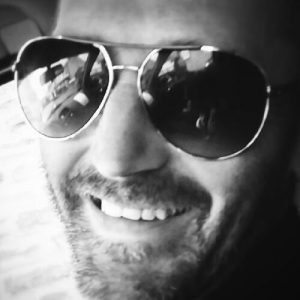
Adam Riley – Angelwest Ltd said: “I sadly never met Nick but his comments & appreciation towards others was second to none and that was just on Linkedin, thoughts go out to the family & friends.”
Mark Parkin – Tiger Scaffolding Ltd said: “I feel like I’ve lost a brother, what a great guy he will be sadly missed in this industry, I got to speak to nick on a daily basis discussing innovation & new product ideas and if I get the chance I will bring them to the market in honour of him and his family.”
The family have asked us to pass on details of Nick’s Funeral arrangements as follows:
A service will be held at Burnley Crematorium at 12pm on Thursday 7th September 2017 All are welcome !
I would like to offer my personal condolences, my thoughts are with Nick’s family, friends and work colleges. Nick will be so sadly missed.
The industry has lost a pioneer. RIP Nick Flynn..
Simian Partner with NTI to Open Oman CISRS Training Centre
Simian Skill International and National Training Institute (NTI) part of the Babcock International Group have joined forces in order to gain CISRS Overseas Scaffolder Training Scheme (OSTS) accreditation for their new centre in the Sultanate of Oman.
CISRS Manager Dave Mosley traveled to Oman back in April for a pre-accreditation visit, Simian/NTI took the decision to source a new location for their new CISRS OSTS practical facility, which is adjacent to another of NTI’s training establishments in the Ghala Industrial Area of Muscat. NTI Business Development Manager Mohammed Atif Uzzaman commented: “NTI Oman are proud to be working in association with Simian Skills and to become the first CISRS approved training centre in the capital (Muscat) which can offer scaffolding programmes that meet PDO’s revised criteria. We are committed to offering world class learning solutions to the Omani market,” said NTI Business Development Manager Mohammed Atif Uzzaman. In a press release CISRS say, The training centre has been fitted out to a very high specification, Simian/NTI has gone to considerable expense to provide new materials and equipment for the centre audit which took place on 9th/10th of August. The new centre boasts newly fitted out air-conditioned classrooms and an on-site restaurant ensure that delegates will enjoy a very comfortable training experience. The investment in the facility has paid off as the centre has gained approval to deliver the following CISRS OSTS courses Level 1, Level 2, Basic Scaffold Inspection and Scaffolding Supervisor training.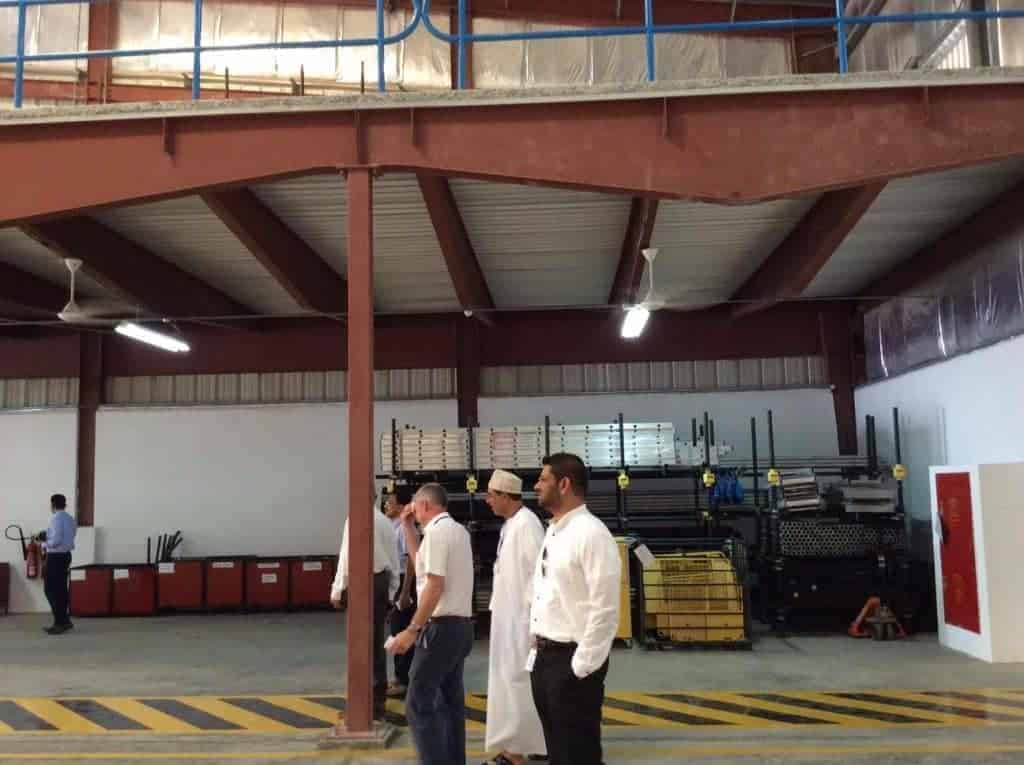
SCA Group Appoints New Industrial Services Director
SCA Group takes on ex-Cape Operations Director, Mark McHale as their Industrial Services Operations Director.
The new appointment comes after significant growth in 2016 for the SCA group and a growing order book in Industrial services in 2017. SCA say Mark brings a wealth of experience to the company with Mark holding previous positions as Operations Director of Cape Industrial Services where he managed over £110m of operation revenue stream and previous to that with Interserve Industrial managing the Industrial services Portfolio.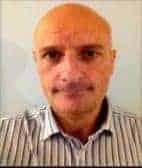
Brickguard designed by Scaffolders hits the market
A new brickguard designed by scaffolders has hit the market and is about to create a storm within the scaffolding industry says it’s makers.
The new brickguard called Sureguard is made from a highly durable polypropylene material that has an unrivaled windspeed resilience. Sureguard is simple and easy to stack and reuse and benefits from eco friendly replaceable hooks. Its maker Alan Clark, Managing Director of Taunton based Montana Scaffolding Ltd explains how and why Suregaurd was created:Like many busy scaffolding contractors we were looking to replace our current stock of plastic coated wire brickguards which were always difficult to handle and visually unappealing. We were looking for a robust brickguard to withstand the day to day rigours of our industry.
The brief was to easily stack for delivery and site storage, be flexible to reduce gaps along scaffolding edges, stand up to severe weather conditions/high winds and save costs.
Nothing we found on the market was assessed to be suitable in all areas, so the decision was made to design our own brickguard, suited to our needs. Perhaps our design would benefit the industry as a whole, as we knew other firms were experiencing similar frustrations which ultimately have an effect on company performance and bottom line.
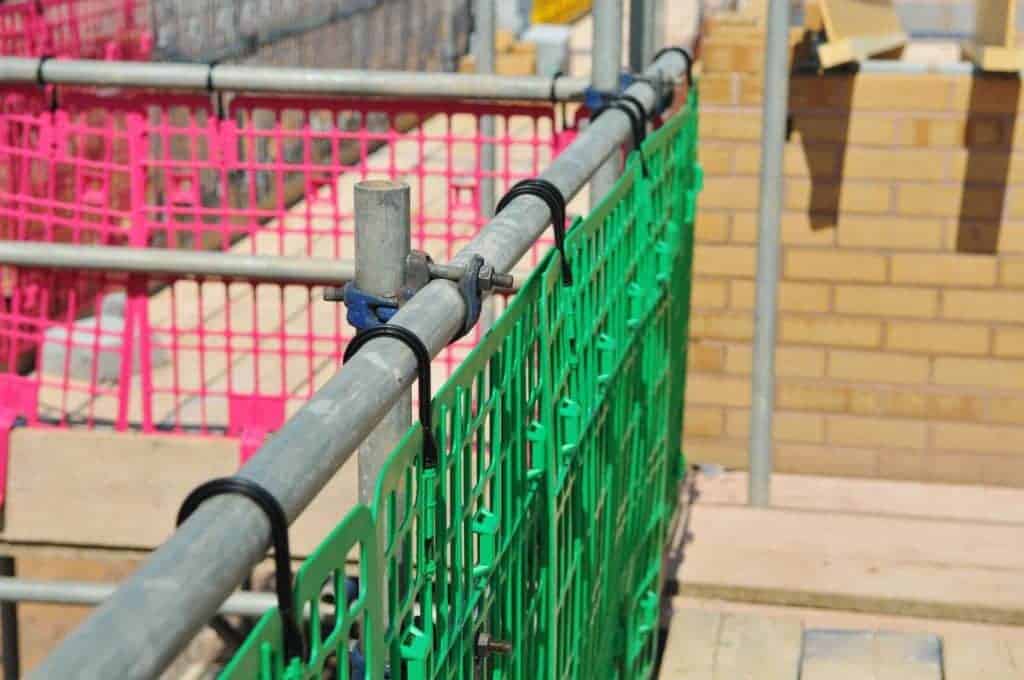
The result of the design process is the Sureguard, a resilient brickguard which exceeded our expectations, particularly when wind-tunnel tested. Whilst achieving an upper wind-speed limit of 78mph the unique patent protected replaceable guardrail hooks stayed firmly attached to the scaffolding. The guardrail hooks are made from strong nylon and are fully replaceable. In the event of any damage occurring to the hooks there is no need to replace the whole Sureguard.
The patented dual toe board restraint clips were undamaged in the wind tunnel; no falling or flying objects. The mesh at the bottom of each panel and the two independent toe clips are designed to enable guards to simply interlock, eliminating all gaps between brickguards and the risks they cause. Sureguards follow the shape of scaffolding, effortlessly bending around corners, fully secured to both sides of toe boards. Fiddly zip ties are not required, reducing associated labour and material costs.
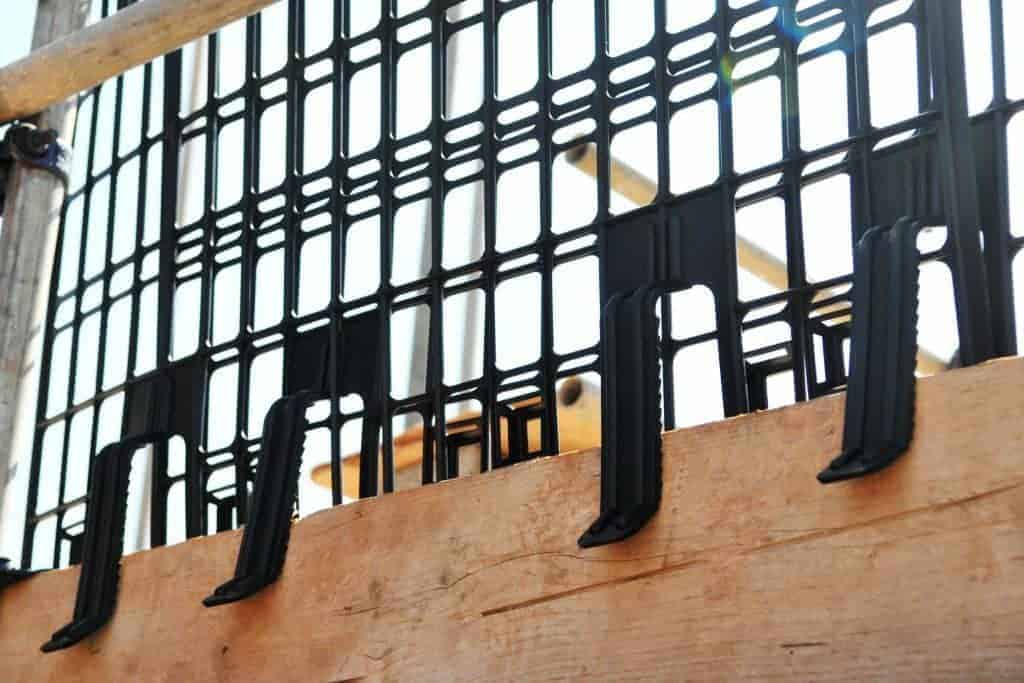
The brickguards are easy to handle and are stackable. The unique moulded shape makes them compact to transport palletised on vehicles and around the yard or site by forklift truck, to reinforce your companies’ commitment to improving site tidiness and safety.
Made from fully recyclable materials Sureguards are available in 7 standard colours – black, blue, red, green, pink, grey and yellow with the option to have your company logo moulded into the plastic for added security when manufactured. For quantities over 2400 units additional colours are available to match your branding.
The Sureguard brickguard is designed and manufactured in the UK to a high standard and is ideal for use in all weather conditions.
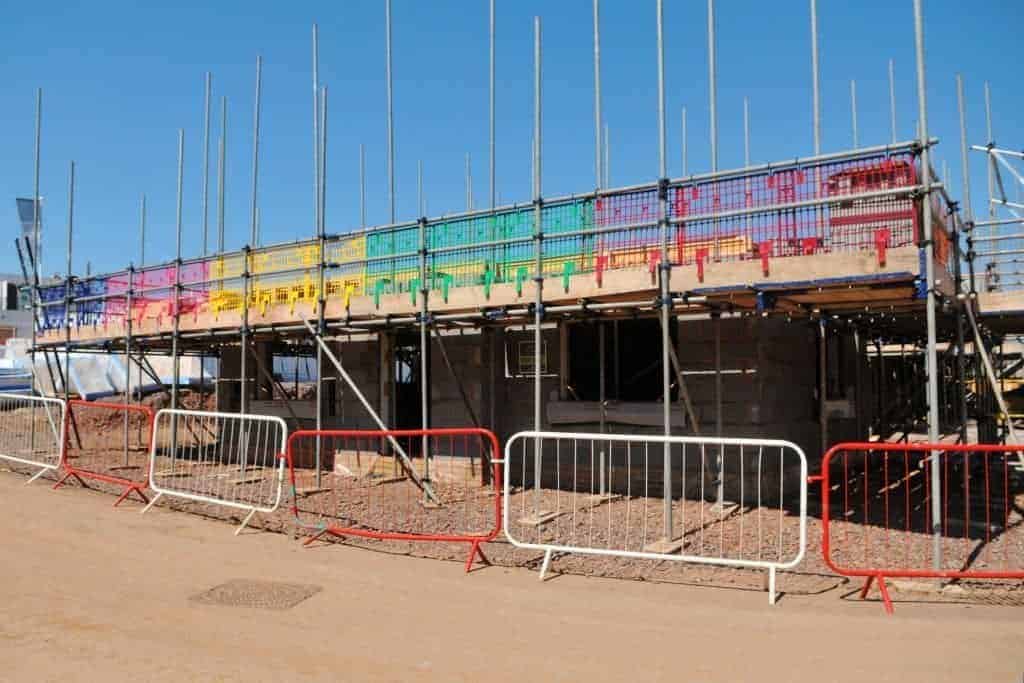
Sureguards exceed our original brief. Bringing them to market now enables other scaffolding companies to benefit from reducing costs associated with waste, labour and brickguard replacement, improved site safety and so much more.
Read more about Sureguard in ScaffMag Quarterly our digital magazine coming soon.