The Voice of Scaffolding Since 2008 | U.K. Edition
Andrew Smith Assumes New Position At Avontus
GKR launches support initiative for Mental Health & Wellbeing
SMART Scaffolder Launches Upgraded Inspection and Handover Apps
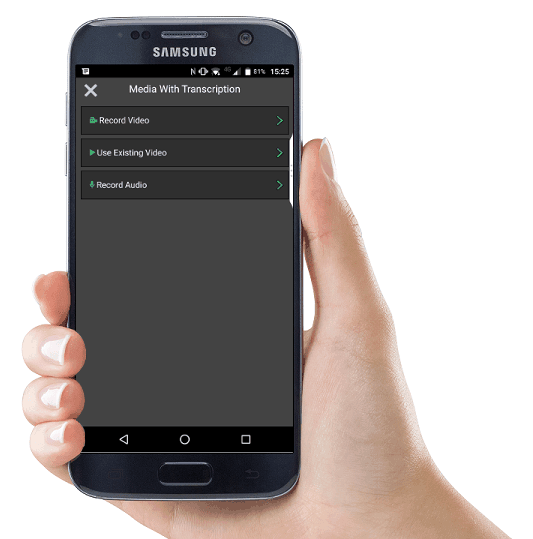
- Record the progress of the scaffold build or dismantle
- Record any problems, such as lack of access or conflict with other works
- Record any variation requests
- Record to show that the site is clear when you have completed the job
- All of this is sent back from the app to the management console, so those in the office can track the progress of the work and be aware of issues.
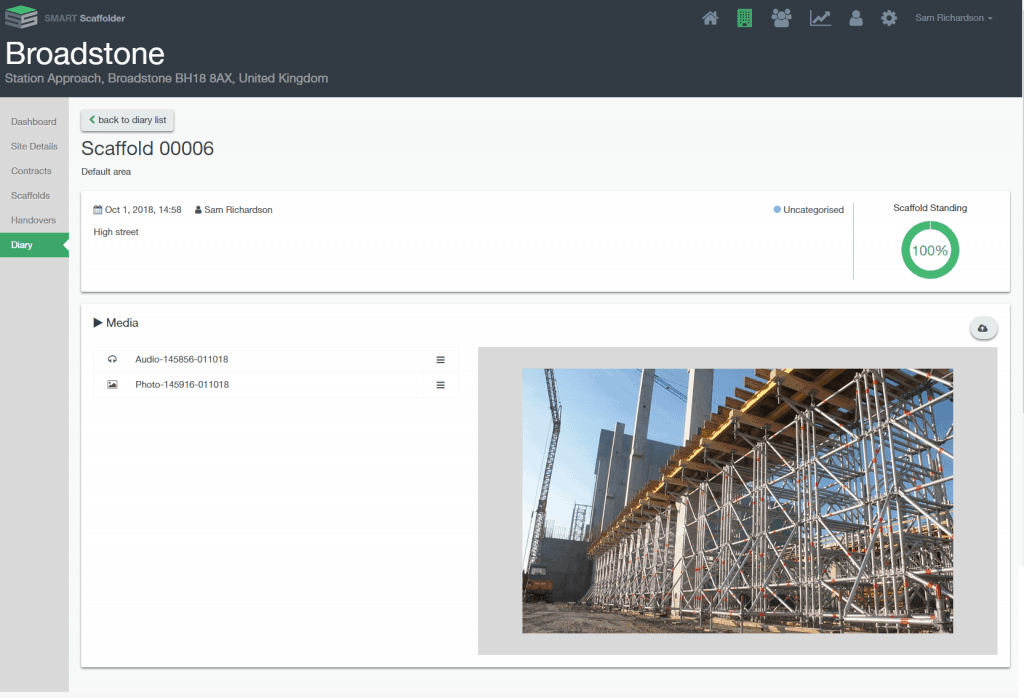
New Identity Revealed as Allied Scaffolding Becomes Allied Access
Allied Access celebrated the launch of its new identity and branding at an event that was designed to make the industry to sit up and take notice.
The North West based Allied Access, formerly known as Allied Scaffolding undertook the rebranding event on Thursday (4th October) to reflect its changing business. Although scaffolding remains at the heart of the business, mast climbers and hoists will now be a significant part of Allied’s access portfolio. With an increasing number of clients choosing a combined approach, and more complex projects demanding a mix of access solutions, Allied Access will now be ideally placed to offer a responsive, efficient and reliable service. Even though the rebrand event had its important message of Allied’s changing business to communicate, its message to attendees of the event also included something the company believes critically important – Safety. Allied Access said inviting Jason Anker MBE as their keynote speaker was a bold move. Jason’s story is without question polar opposite to being uplifting. Confined to a wheelchair after a fall from an untied ladder, Jason’s mission is to raise awareness and to help prevent what happened to him happening to anyone else. However, there were light-hearted moments at the launch event provided by guest speaker Barrie McDermott, Rugby legend and Sky Sports pundit, who entertained guests with his trademark blend of insight and entertainment. Pete Ferris, Allied Access’s Commercial Director said: “Our new identity is bigger, brighter and bolder, reflecting the business we are now and the business we are going to be. The launch event was a great success and it was fantastic to see so many of our clients attend. For some, it was the first time they had heard about our humble origins. “We’ve changed a lot since the early days back in the 1980s, and we’ll continue changing to meet the needs of our clients.”First CISRS Approved Scaffolding Training Centre Opens In Doha
Interserve sells Scaffolding and Painting Division
Interserve has entered into an agreement to sell its industrial scaffolding and hard services business for £3.6m to Enigma Industrial Services Holdings Ltd.
The division being sold provides scaffolding services to housebuilders and other contractors as well as its SIP (Scaffolding, Insulation & Painting) services to large industrial sites.
Interserve says the £3.6 million purchase price is payable upon completion with the potential for a further cash injection of £1 million subject to the Business achieving certain financing targets for the financial years 2018 and 2019. The money from the sale will be used to reduce Interserve’s debt.
For the year ended 31st December 2017, Interserve Industrial Services Limited (IISL) reported an operating loss of £4m and had gross assets of £47.3m. The transaction will result in a loss on disposal of £8.4m for Interserve.
Together with the closure of IISL power activities earlier this year, this sale concludes Interserve’s exit from its industrial contracting activities.
Managing Director Scott Hardie holds on to his position and will continue to lead the business. Debbie White, Chief Executive Officer at Interserve said: “We are pleased to announce the sale of the access and hard services business as part of Interserve’s strategy to focus on core customer segments.”HAKI Scaffolding Unveils New Stair Chart
- HAKI Symmetrical Stair Tower, now in Mk2 revised format.
- HAKI Public (& Events) Access Stair Tower (PAS), released in 2018.
- HAKI Compact Stair Tower, updated in 2018. &
- HAKI Traditional Stair Tower.
- HAKI Twin Stair Tower.
Nuclear plant Hinkley Point C continues to power ahead
New photos and film footage released by EDF shows the scale and construction progress of the new nuclear power station.
The construction of Hinkley Point C began two years ago after the government signed a deal with French firm EDF and its Chinese partner CGN. More than 3,200 people are now working on the project in Somerset. EDF has said it would be a ‘significant moment and major milestone’ when a 4,500 tonne concrete platform supporting the reactor buildings was completed in 2019. The project is also setting its sights further ahead with preparation for the MEH phase (Mechanical, Electrical and HVAC – heating, ventilation and air conditioning). Yesterday (Thursday 27 September) four major UK contractors signed the “MEH Alliance” to work together on the complex installation of cabling and pipework in the power station’s 2,500 rooms. The innovative approach means that Altrad, Balfour Beatty Bailey, Cavendish Nuclear and Doosan Babcock will pool their expertise to work as a single entity. The alliance aims to create new industrial capacity and jobs by manufacturing specialist pipework in Britain.Video: Motorbike rider wiped out as scaffolding falls four storeys
The Mail reports the footage was captured on CCTV in the Sultanpet area of Bangalore, India. As the 38-year-old rider, known only as Chandan, rode to his office on August 31 the film shows how the piece of scaffolding knocks him out.
His helmet flies off and he falls to the floor while shocked onlookers rush to his aid.
The man was rushed to a local hospital. Despite the horrific accident, his condition is said to be improving under the care of hospital staff, who say that he is now out of danger.