The Voice of Scaffolding Since 2008 | U.K. Edition
35-storey scaffolding demolished by mother nature
PERI provides unique scaffolding solution at Farringdon Station
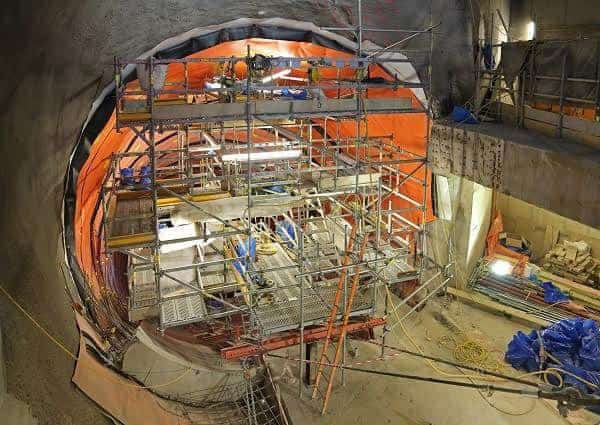
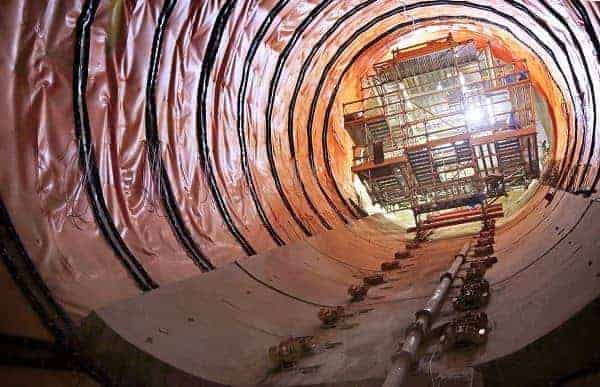
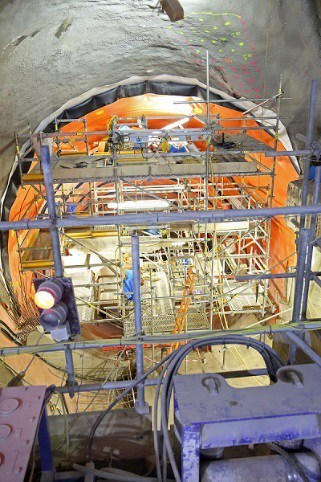
Search underway for man missing from North Sea Rig
A search is still underway tonight after a man was reported missing from a North Sea rig.
The 49-year-old man who, according to unconfirmed reports on social media is a scaffolder from the Aberdeen area. The man was reported missing at around 9:20pm yesterday from the Noble Lloyd Noble installation, located in the Mariner Field approximately 90 miles (150km) east of Shetland.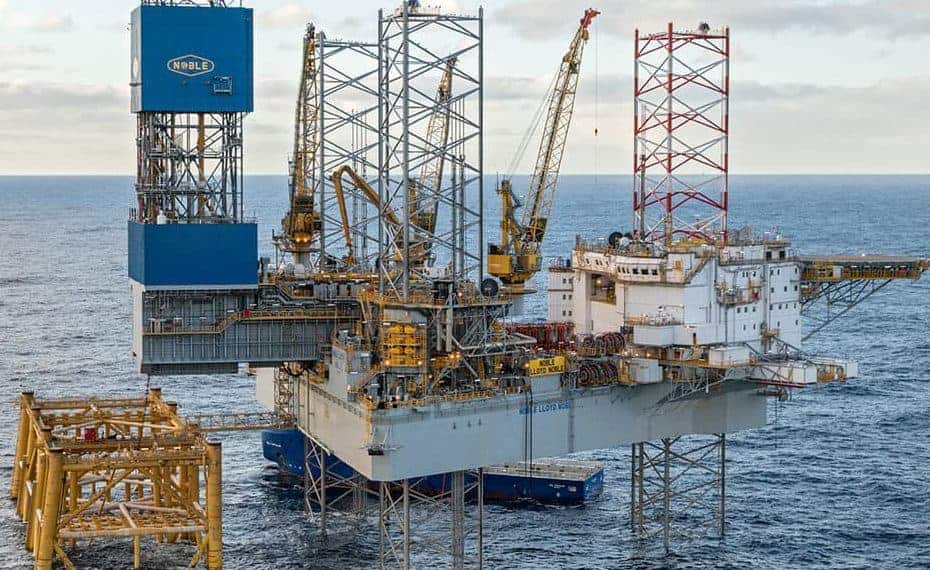
TRAD’s people supported Workers Memorial Day
TRAD’s people and many of their clients – including Walter Lilly – supported Workers’ Memorial Day, held on Friday, 28th April 2017.
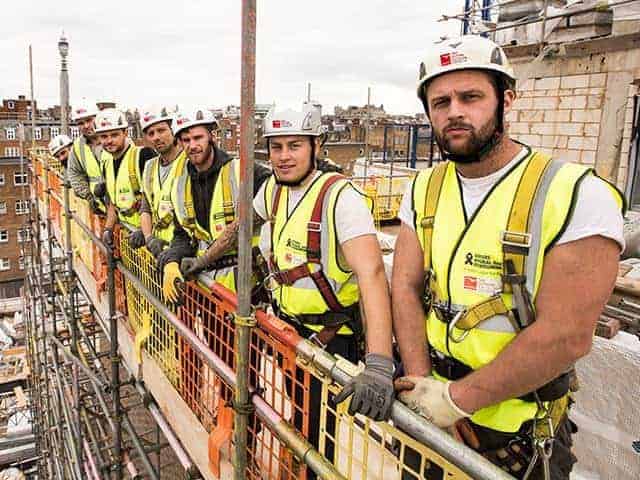
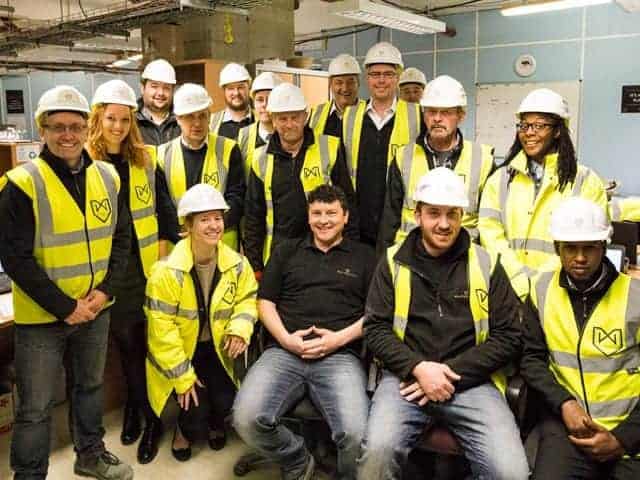
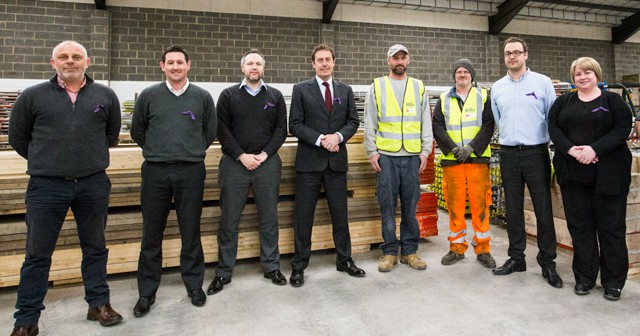
Generation Launches New Design Service
- A highly skilled estimation, design and engineering team
- State-of-the-art design software
- Project support and financial assistance
- On-site surveys
- Hand sketches
- Working CAD drawing production
- Stress and structural analysis
- Estimation
- Material shipping and health and safety advice
- Equipment solutions based on scaffold and access requirements
Scaffolding collapse narrowly misses school children
School children and staff narrowly miss serious injury after scaffolding collapses onto a school in Wales.
An investigation by Health and Safety and Vale of Glamorgan Council officials is underway after scaffolding collapsed on to the main entrance of Albert Primary School in Penarth, Wales on Friday 5th May.
Reports suggest the scaffolding was erected on a neighbouring property and came down in high-winds. Amazingly no children or staff at the school were injured.
One parent said “My wife and kids had walked through the gate moments before the scaffolding came crashing down. A very close call”.
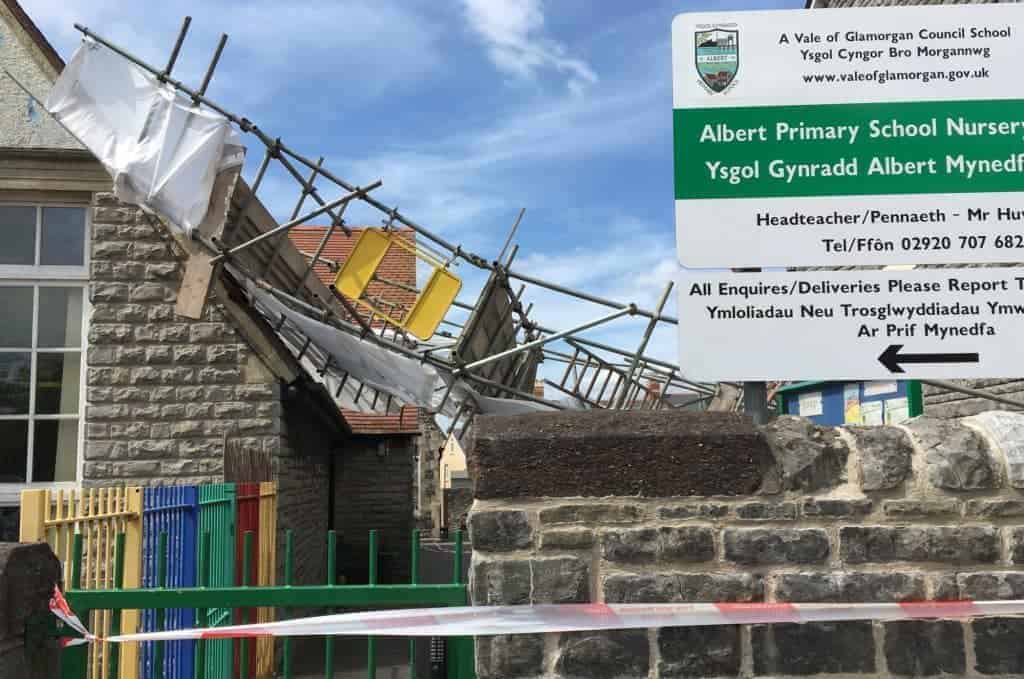
Albert School issued a statement to parents saying “Please be made aware that the Top Gate of the school is not accessible today due to a neighbouring property’s scaffold falling across into the school premises.
Please be assured no one was injured in anyway. Due to restorative works taking place there will be considerable congestion at the end of the day.”
Planet Platforms Flying high for the Yorkshire Air Ambulance
Planet Platforms has pledged to keep their sponsorship of the life saving YORKSHIRE Air Ambulance (YAA) going beyond the company’s 40th anniversary.
As one of the world’s leading manufacturers of working at height equipment the Wakefield headquartered business, has been proud of their relationship with the YAA. A key maintenance provider for the two helicopter operation, they also see their role as giving something back to the community. With this in mind, the team will be organizing a series of fund raising activities, as well ensuring YAA’s maintenance costs for another 12 months. MD Peter Pemberton said: “Yorkshire Air Ambulance ethos of protecting those in danger resonated with our founding principals. Planet Platforms has worked with Air, Sea and Rescue and the YAA for many years so it seemed logical to support them in our anniversary year. YAA is an independent charity operating two helicopters out of Nostell Priory in Wakefield and North Yorkshire. Being on our doorstep they were an obvious choice for our anniversary year charity. It costs £4.4m each year to keep both aircraft flying and provide the valuable service the public relies on. We have already planned a series of fundraisers throughout the year in addition to the sponsorship and would urge everyone to support them.” As a rapid response air emergency service the Charity serves a population of approximately five million people across four million acres. Planet Platforms makes bespoke working at height solutions and off the shelf scaffolding for major aviation, defence, rail, offshore and construction companies around the world. It was keen to mark its celebration by reflecting its core values.HSE Inspector Numbers Cut By A Quarter
Numbers of Front-line health and safety inspectors have been cut by 25 per cent in six years according to figures obtained by the Unite union.
In 2010 the total of inspectors stood at 1,311, but by the end of 2016 this had fallen to just 980. These shocking statistics emerged from a Freedom of Information request in the run up to International Workers’ Memorial Day. This news comes amid revelations acquired from the same source revealing it takes three years four months on average, for any sentence to be handed down after a workplace fatality. Clearly the findings are worrying for industry professionals. “HSE inspectors play a vital role in keeping workers safe,” said Unite acting general secretary Gail Cartmail. “Rogue bosses who are prepared to break safety laws, are only kept in check by the fear of being caught and punished. Fewer inspectors mean more bosses willing to risk workers’ lives to boost profits. In these circumstances it is more important than ever that union safety reps are given the training, support and time to conduct their duties and keep their fellow workers safe.” The Health and Safety Executive is the body responsible for the encouragement, regulation and enforcement of workplace health, safety and welfare. It also carries out vital research into occupational risks in Great Britain. As part of its work HSE investigates industrial accidents, small and large, including major incidents. Both Unite and workers in the construction industry will be watching the situation closely in the hope things will improve going forward in terms of growing health and safety inspector numbers going forward.Contractor Fined More Than £200,000 Over Tragic Death of Scaffolder
Steel Fabricator CMF Ltd has been ordered to pay more than £200,000 following the death of a scaffolder crushed by a falling concrete block in London four years ago.
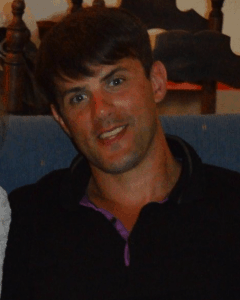
GKR Scaffolding in partnership with BT Motorsport
Bobby Thompson aims to reach new highs in 2017 in the Milltek Sport Volkswagen Racing Cup championship with support from his headline sponsor GKR Scaffolding Limited.
As the hotly contested Milltek Sport Volkswagen Racing Cup rolls towards the Rockingham Motor Speedway in Corby, Bobby Thompson is delighted to announce that GKR Scaffolding based in London and Kent, will be Title Corporate Sponsor of the #19 Team Hard VW Golf for the rest of the 2017 Bobby’s familiar black and orange Golf GTI R Cup race car will now sport the GKR Scaffolding livery and logo, as seen on their iconic fleet of trucks. It also displays the ‘Better Future’ branding – a programme that GKR will be launching to focus on helping the construction industry, GKR employees and local communities build a better future.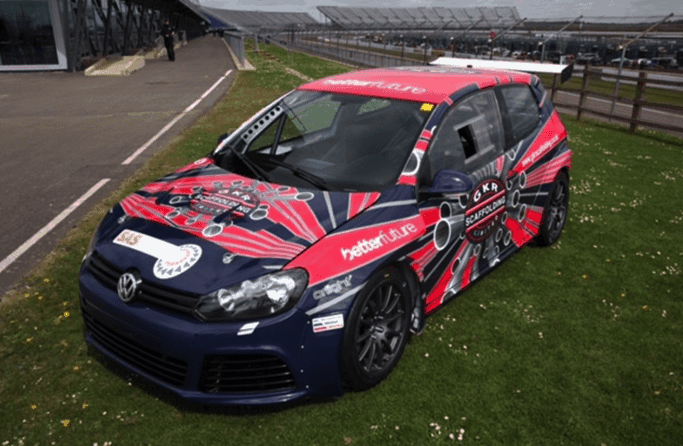
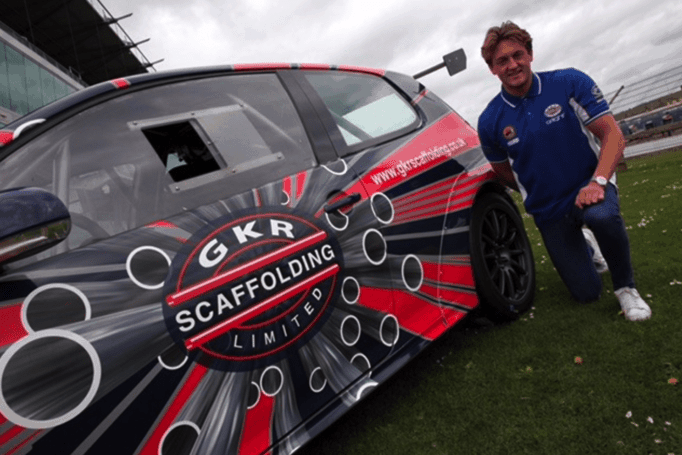