U.K. Edition
HSE Restarts Site Inspections
The Health and Safety Executive has announced it’s resuming with construction site inspections.
As the construction industry in England begins to return to work after lockdown the HSE has announced its resuming site inspections. The regulator has said it’s adjusting the focus of its activities including visits to business premises and sites which will be conducted in line with social distancing regulations and guidelines. The HSE’s activities will continue to be guided by the specific requirements and characteristics of the sectors it regulates and in line with advice from the UK Government and Public Health Bodies. The HSE has stated it will:- continue to work closely with, and across, industry sectors to enable businesses to put practical measures in place to help people get back to work safely, while remaining compliant with public health and health and safety at work requirements
- will carry out work to check that appropriate measures are in place to protect workers from COVID-19
- will resume targeted proactive inspection work of high-risk industries
- will continue with, and will build on, our re-prioritised regulatory approach to key critical areas and activities in major hazard offshore oil and gas and onshore chemical, explosives and microbiological industries using remote techniques in conjunction with site visits, including conducting visits offshore
- will continue to undertake regulatory activities which do not require site visits as normally as possible, for example Approvals and Authorisation work for biocides and pesticides, Statutory Permissioning activities such as Licensing, Safety Case / Report Assessments, Thorough Reviews, Combined Operations Notifications, Wells Notifications, Land Use Planning Applications, Hazardous Substances Consents etc
- continue to investigate work related deaths across all industry sectors, the most serious major injuries and dangerous occurrences and reported concerns, including those related to social distancing and COVID-19. In such cases we will continue to secure compliance with the law, and conduct our investigations using a mixture of technology, without compromising the collection of evidence and our ability to secure effective control of risk, and site visits.
Safety & Access Set To Restart Training
Safety & Access is poised to reopen after implementing a raft of COVID-19 safety measures at its UK centres.
The Nottingham and Immingham based scaffolding training provider has developed strict procedures for training including regular temperature checks for all candidates as well as clear guidelines on social distancing, hygiene, and welfare requirements. The training firm has said it will be taking a limited number of bookings that will commence from the 1st of June. However, due to social distancing requirements, the maximum numbers allowed for each course will be at a significantly reduced level. Its looking to give priority to its existing customers that had courses postponed during the initial lockdown period first choice for the scheduled training. The Safety & Access offices are now open with a limited number of staff to deal with outstanding enquiries on qualifications and general requests. Rick Statham Safety & Access joint Managing Director told ScaffMag: “We are pleased to confirm that we will be offering limited training support for our customers from June at our Nottingham and Immingham training centres. The safety of staff and customers is our highest priority and we have developed and implemented precautions and guidelines to ensure that risks are reduced and are in accordance with government and industry guidelines. We have received clear intentions from our customers that ongoing training is critical and we are doing our utmost to meet those needs. Due to important social distancing requirements, our candidate numbers will be significantly reduced and we will be working to ensure the best available support service.” The CISRS registered scaffold training provider has been closed since 24th March.Coronavirus Site Operating Guidance Updated For Fourth Time
The Construction leadership Council has scrapped the 15-minute limit for contact between construction workers in its latest version of the coronavirus site operating procedures.
The fourth version of the document which was published on Tuesday has been updated to incorporate a number of technical changes following the recently published government guidance on Working Safely during Coronavirus (Covid-19). One major u-turn within the guidance is the removal of the requirement for face-to-face contact to be kept to 15 minutes or less. The section on PPE now also links to the latest Government guidance on face coverings. Other changes include:- References to one-way systems and the reconfiguration of seating and tables and an update on portable toilets
- The requirement to share risk assessments with the workforce
- Clarification on when to travel to work, as set out in the Government’s COVID-19 Recovery Strategy
- Updated links and wording on social distancing
75 Years of Layher
This year marks the 75th anniversary of one of the world’s finest company exponents of scaffolding. Given all of their incredible achievements, ScaffMag takes a closer look at Layher in a year like no other.
From the Cathedral of Saint Mary of the Flower to the Northern Black Forest National Park, The Duvha Power Plant to the Duisberg Rollercoaster structure, and the world-renowned Elizabeth Tower aka Big Ben, the world has been blessed by the expertise of Layher.Leading The Way
Wilhelm Layher GmbH & Co KG explained: “This year we can celebrate the 75th anniversary of our company. We’re very happy about that – and proud of it too. But this anniversary for Layher has only been possible because our customers have been putting their trust in us every day – in some cases already in the third generation. “We have quite deliberately chosen the motto “75 years of future” for our company anniversary. After all, our orientation towards the future is one of the key factors in Layher’s success. Nevertheless, such a special event as the company’s 75th anniversary naturally invites us to pause for a moment and celebrate this milestone in our company history together. “Every single person contributes to Layher’s success day after day at his or her workplace. We would, therefore, like to thank you from the bottom of our hearts: for your great commitment. For your competent and conscientious cooperation. And for your loyalty to Layher.”A Driven Aim
The aim of Layher has always been the success of its customers, in close partnership and never in competition to them. But there’s little doubt their innovative system solutions are a key focus of product development. Take the Aluminium FlexBeam for example – following the award of the French innovation prize “MAT D’OR” in the “Equipment and Tools” category, the Layher FlexBeam was also given the accolade of “Innovation of the Year” at the annual ball of the UK’s “National Access and Scaffolding Confederation” (NASC) in front of more than 700 guests.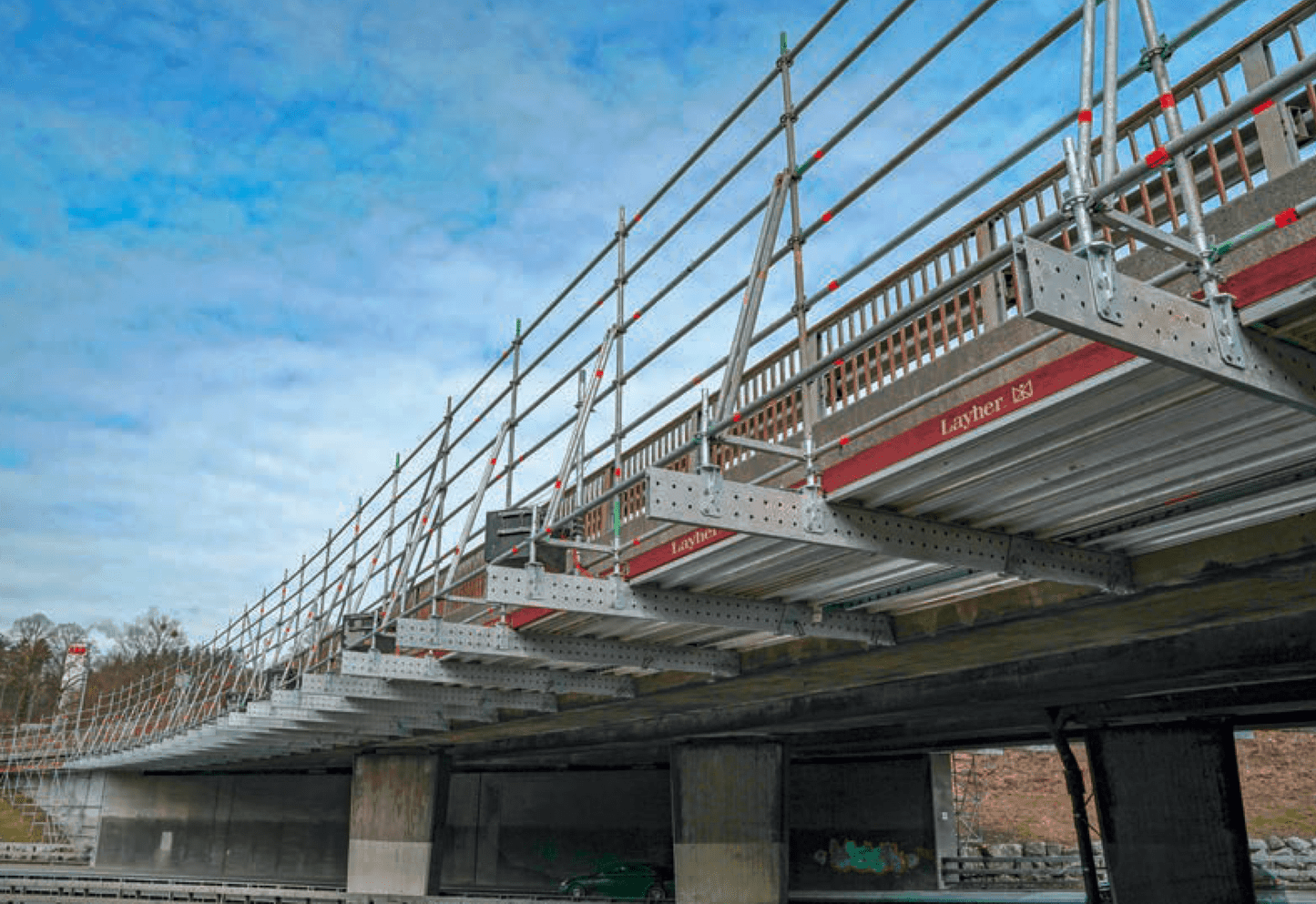
Stairway Specialists
Layher also provides, with some supplementary parts to its Allround Scaffolding System the globally requested and therefore accepted emergency stairways. These innovative escape stairtowers satisfy all legal requirements of width and load-bearing capacity, as well as human and material safety. Extremely environmentally aware, Layher has an energy efficiency 10-year goal involving 10% lower energy consumption per unit produced. This also includes selective planning in production to reduce CO2 emissions, the selection and acquisition of ecologically sustainable raw materials – only those suppliers with ISO certificates are picked. Only machinery from the highest energy efficiency class is used, with technologies and efficient processes in the production ensuring preservation of resources and of course top product quality. The list goes on.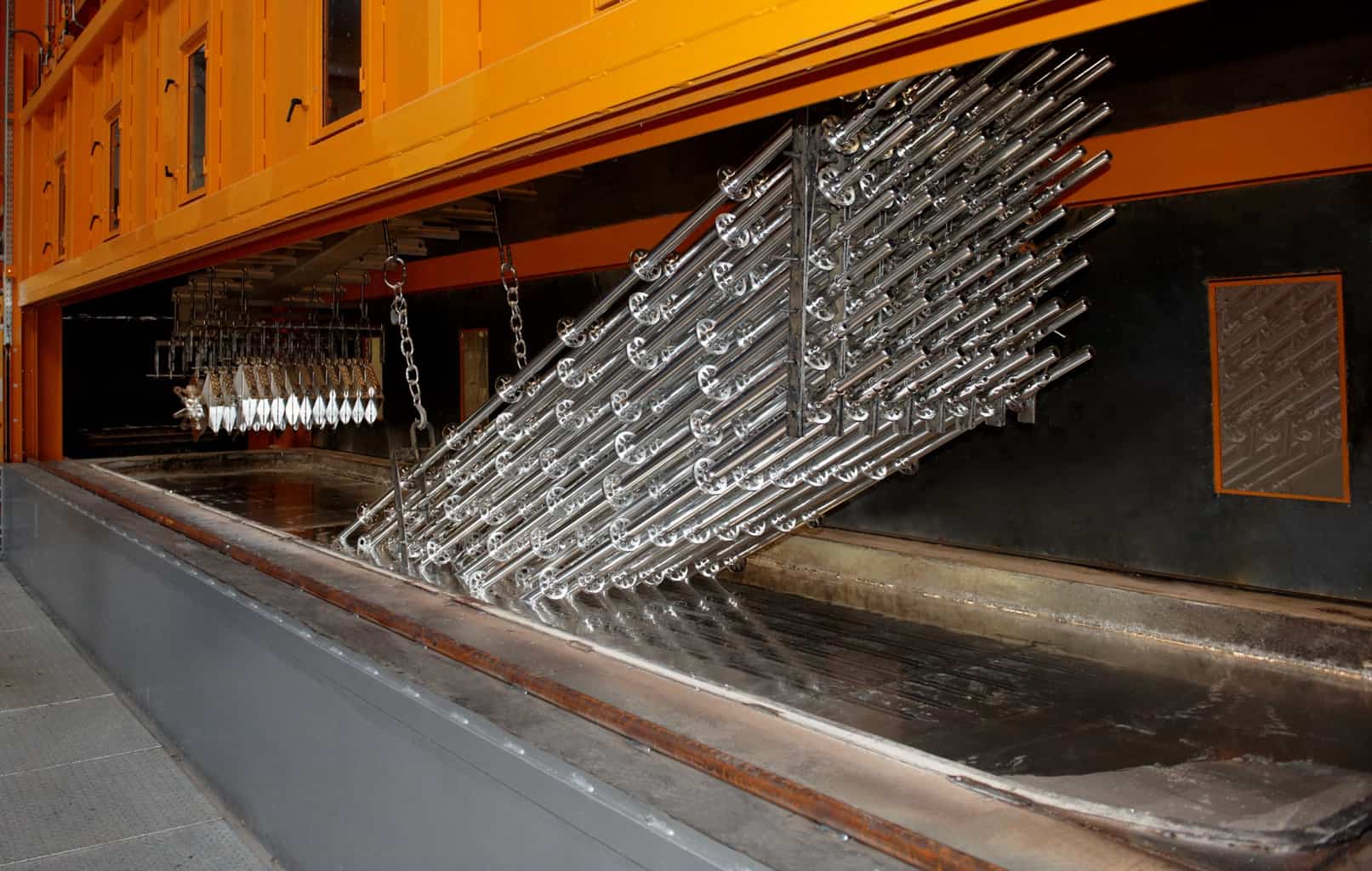
Impressive Awareness
Layher has always acted with awareness and attention to economic and ecological sustainability both in its products and working processes. In terms of social responsibility towards clients, employees and society as a whole, they really have been first class. Layher explains: “We’d like to create more possibilities for you with innovative system solutions within the framework of the Layher Lightweight philosophy. This offers more safety, more ergonomics and above all more profitability at the site. High-quality products in conjunction with the generation-spanning compatibility of Layher systems, provides protection to customers’ investments, no matter which generation of product they purchased. “We can present competent advice, detailed technical documentation, training and seminars, plus support in the issue of digitalisation with Layher SIM and the integrated software solution LayPLAN SUITE.”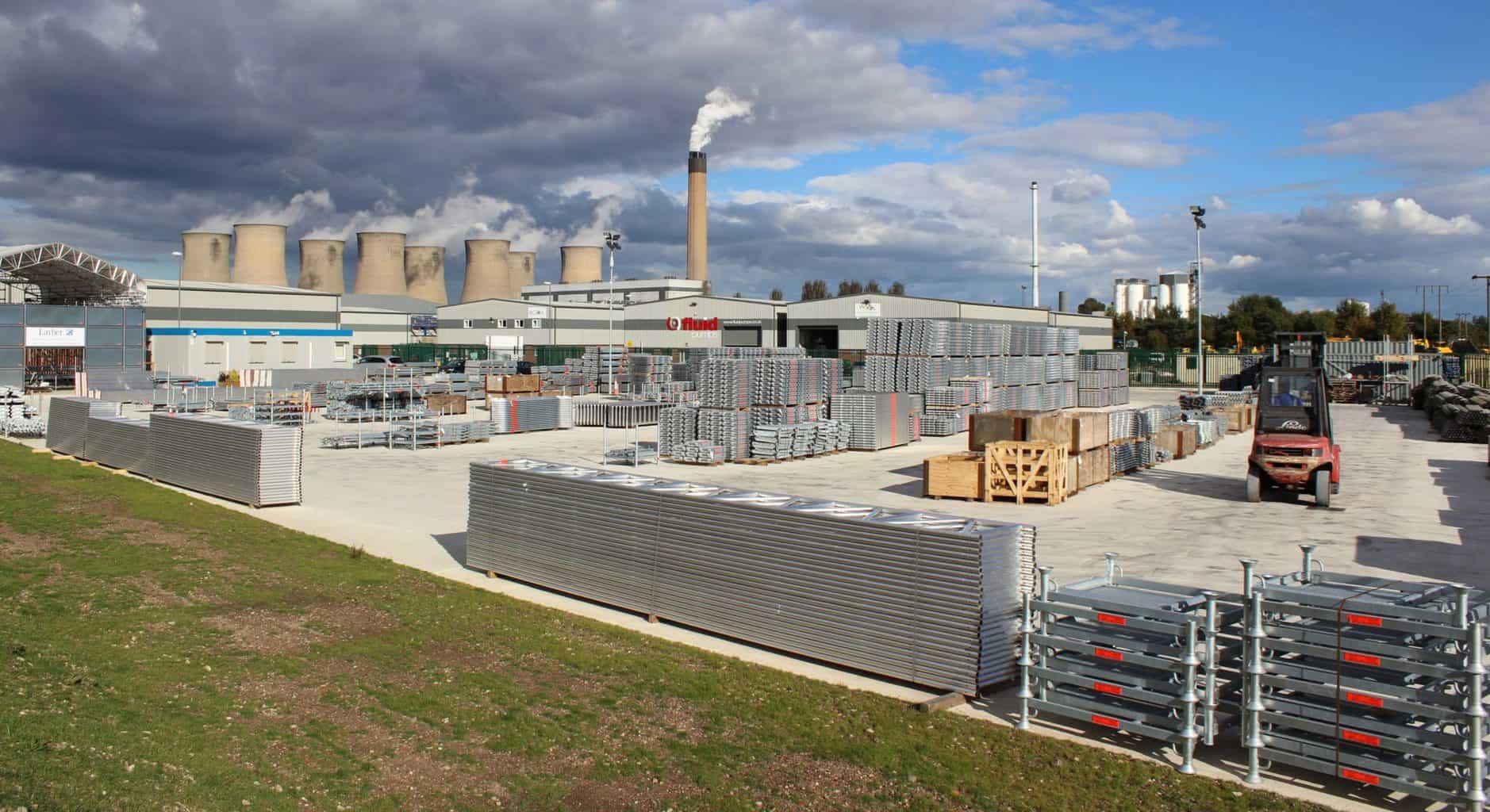
Layher SIM
In terms of the Layher SIM Roland Hassert, Head of Construction, Application Technology at Layher GmbH & Co KG added: “The Layher SIM consistently transfers the BIM principle to scaffolding. It is also helpful in non-civil-engineering projects and, more importantly, a practical addition to any project because it reduces costs, improves safety and increases commercial viability.” Scaffolding Information Modelling – or SIM – is a smart 3D-modelling process. SIM enables scaffolding companies to plan, build and manage temporary scaffoldings more efficiently, and also provides access to BIM (Building Information Modelling). Layher’s LayPLAN SUITE provides customers with an effective tool for the SIM process.Influencers In Action
Remember – Since the company was established in 1945, Layher has been continuously evolving, innovating and providing the best and original product solutions to scaffolding construction. Its ideas, and in some cases collaboratively with their customer partners have influenced development to an enormous extent. The practical benefits this dynamic company provides really are to be admired – it seems clear they remain innovators in a rapidly changing industry. For those clients looking for the best in experience – 75 years and counting tells anyone all they need to know about their expertise. Happy Anniversary Layher. www.layher.co.ukScaffolding Training Set To Resume
Scaffolding training provider Simian is set to re-open its centres on the 1st of June with a pilot week aimed at testing the water before looking at a full delivery of their services.
According to Simian, Their plan is to have one course running each day during that week to check the arrangements they have implemented with eventual full function in mind. If all goes well the company hope to steadily ramp back up to a new normal of scaffold training provision. Dave Randles, Operations Director And Principal Consultant at Simian told us: “The arrangements we are implementing include physical amendments to the training centre. These will include additional washing facilities, sanitization stations and layout changes to classrooms, site entry and exit processes. This will include a brief questionnaire and temperature readings for delegates. “Social distancing will be maintained and there’ll be the implementation of a one-way system in common walkway areas, temporarily reducing the centre’s overall delivery capacity, until we can ensure we can operate safely under the new measures.” In addition, only customer-facing staff will be required to work at the centres as other support staff continue to be home-based.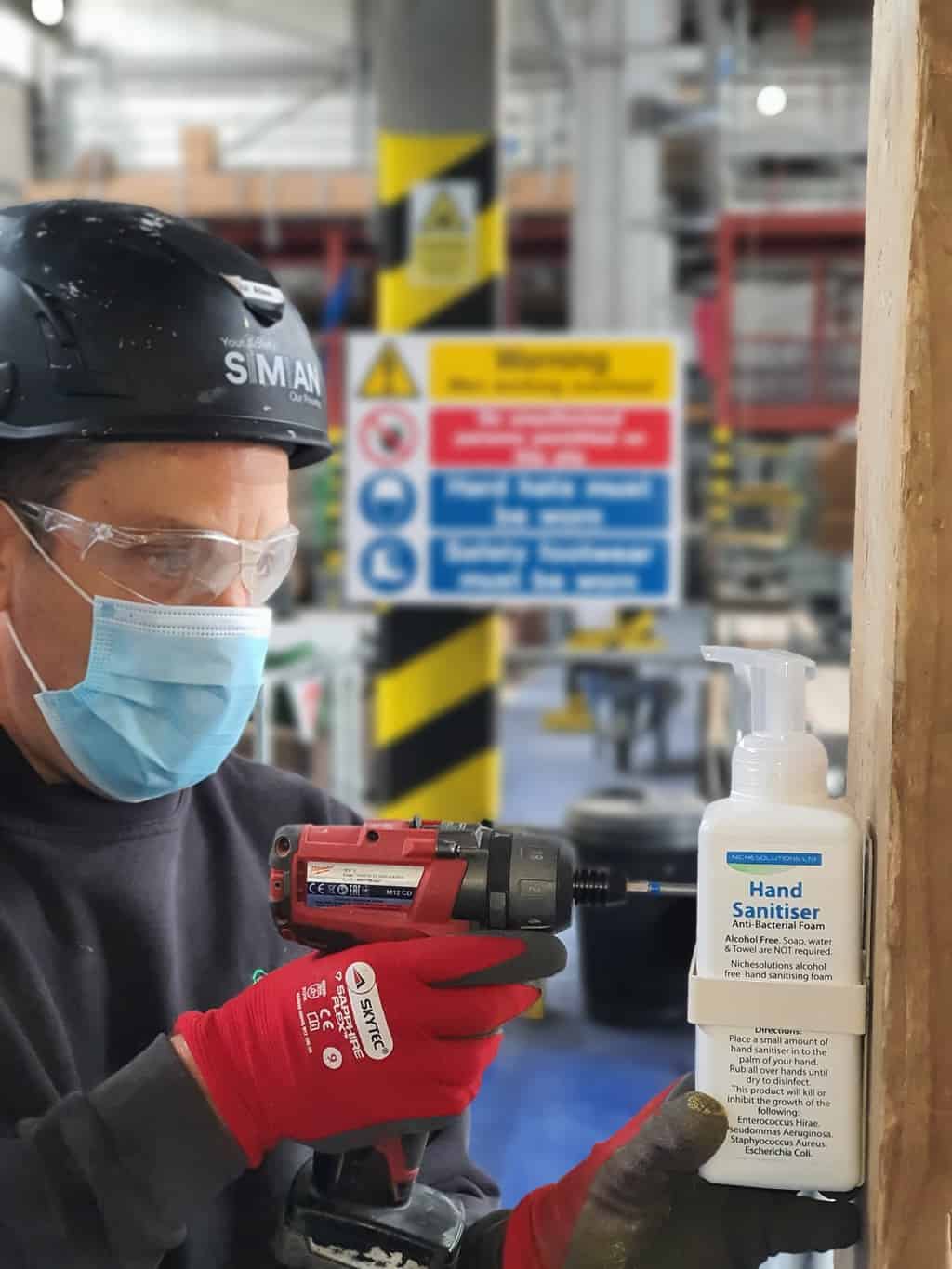
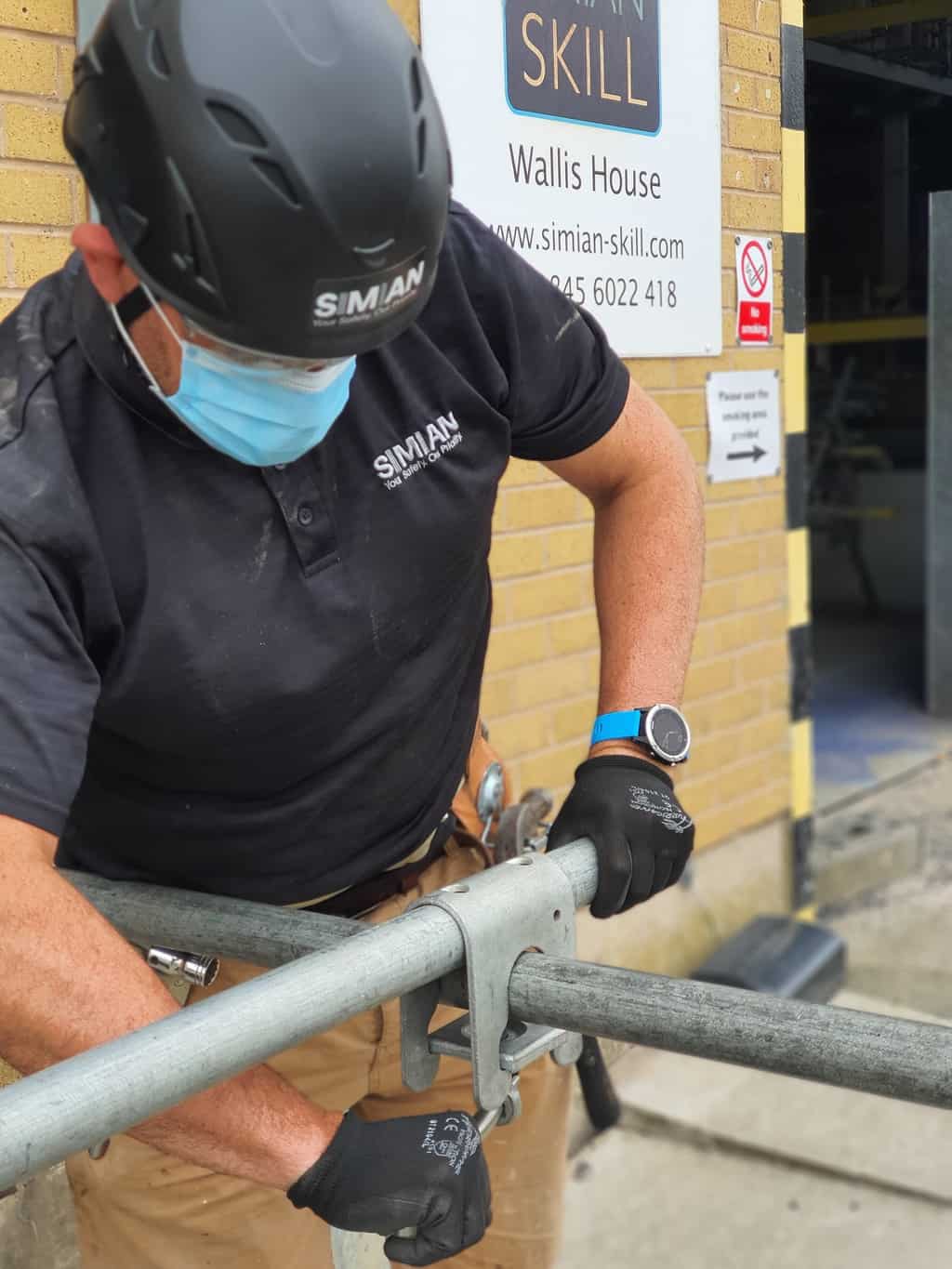
Altrad Services Bags Multi-Year Contract at Fawley Refinery
ExxonMobil has awarded Altrad Services a multi-year contract for the provision of access, insulation and painting services at Fawley refinery near Southampton.
The new contract, which commenced on the 1st May 2020, builds on the firms previous contract which encompassed ExxonMobil and Altrad working in a collaborative manner, to deliver a value-enhancement programme over a five-year period. The performance on the contract was recognised in 2019, when Altrad and ExxonMobil received the “Company Collaboration Award” from the Engineering Construction Industry Association (ECIA). Chris Parsons, Altrad Services Portfolio Manager, commented: “During the past five years, we have worked tirelessly with our colleagues at ExxonMobil to deliver greater productivity and introduce measures to improve the overall efficiency of our service delivery. In 2018, we integrated the access, insulation and painting teams with our mechanical services teams to provide a seamless delivery capability for ExxonMobil operating under a single Altrad management team. ” The award of the access, insulation and painting contract provides continuity of employment for around 150 Altrad staff, and when added to our other contracts on the refinery, supports an overall site team of over 200 personnel.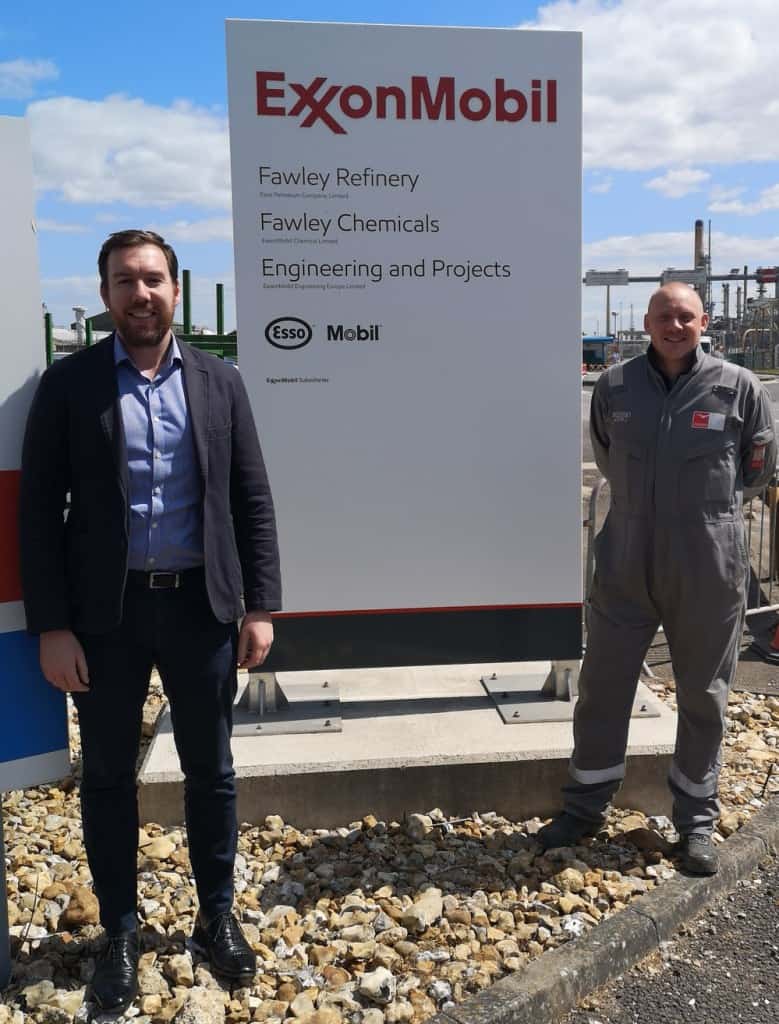