The Voice of Scaffolding Since 2008 | U.K. Edition
New Contracts Director appointed at Rilmac Scaffolding
Winner of the NASC Scaffolding Product Innovation Award announced
The winner of the inaugural NASC Scaffolding Product Innovation Award has been announced at the confederation’s AGM as Acorn Scaffolding (Yorkshire) Ltd – for their impressive £1.8M 50m (w) x 20m (h) x 90m (l) ‘Acorn Super Structure’ temporary roof at the Creamfields Steel Yard event this Summer.
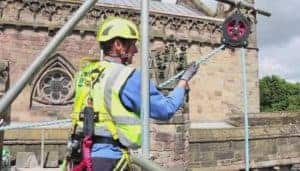
And a highly commended NASC Product Innovation Award has been given to TRAD Scaffolding Co Ltd for their revolutionary ‘Big Ben Braked Gin Wheel’ – designed to stop scaffolding loads plummeting from height.
There were eight entries for the inaugural biennial NASC Scaffolding Product Innovation Award – launched this Summer to celebrate the very best developments in new scaffolding materials and products from inventive NASC members at the forefront of change in the UK scaffolding industry.
The entries were considered by an independent judging panel (Rick Statham of Safety & Access Ltd and Simon Hughes of Simian Risk Management Ltd), with NASC Technical Officer, Ken Johnson the point of contact for judging:
- Acorn Scaffolding (Yorkshire) Ltd for the ‘Acorn Super Structure’
- TRAD Scaffolding Co Ltd for the ‘Big Ben Braked Gin Wheel’
- Malvern Scaffolding Ltd for their ‘Malvern Key-Tie’
- Layher Ltd for the new Universal Aluminium HD Beam
- HAKI Scaffolding Ltd for their cutting edge HAKI Decking CADEE system
- TRAD Hire & Sales Ltd for the Plettac Metrix Permanent Advanced Guardrail
- GKR Scaffolding Ltd for their new Elimin-8 innovative scaffold fitting, and
- Focus Scaffolding Ltd for their two and three board hop-up bracket for tube and fittings.
The winners were announced at the NASC AGM in Amsterdam, on Friday November 25th, where trophies and certificates were presented. And in addition Acorn and TRAD will now be able to use a bespoke NASC Product Innovation logo for a period of two years.
At the AGM, Des Moore, NASC Vice President and Chair of the NASC Hire & Sales Committee gave a presentation on the various entries, showcasing cutting edge products to the membership and the scaffolding industry as a whole.
Speaking about Acorn Scaffolding (Yorkshire) Ltd, the judges said: “Acorn came through in creating an innovative structure using an innovative product. Their aim is to help clients deliver world class, unique and memorable events –specialising in innovative, temporary scaffold-based event structures. Their brief was to push the boundaries of festival production.
“It took months of collaboration, planning and design. The effect was to give every festival goer enjoyment of the premium technical production and high end immersive technology. It is an exceptional product borne out of determination to reach solutions in close liaison with a manufacturer and client. The judges made their determination considering the project as innovation at its best.”
Runner-up, the TRAD Scaffolding Co Ltd ‘Big Ben Braked Gin Wheel.’ was highly commended for its wide-reaching benefit, ensuring that loads do not go into free fall, and for radically reduced rope chafing characteristics.
The judges said: “By applying designs from other industries to our trade and enhancing the safety of this commonly used lifting accessory, TRAD evolved this clever item through their in-house ‘Play it Safe’ safety meetings. It was seen as a major benefit to the whole of the industry – ensuring loads cannot plummet, which is a real innovation and safety feature.
“This product will undoubtedly ensure a reduction in handling injuries. Even hoisting upwards allows fluid movement and safe landing of materials – solving a major safety feature that is a common ‘near miss’ situation. It will assist in significantly ensuring safe practice and helping to ensure operatives go home safely to their families at the end of the day.”
NASC MD Robin James said: “This new biennial award has attracted considerable interest and has been superbly supported by the NASC members. It shows the ingenious and inventive nature of our membership – who lead the way with scaffolding product innovation, for productivity and safety. Credit should go to all of the nominees and the hard working members of our hire and sale committee, who pioneered this excellent scheme. And particular congratulations go to the inaugural NASC Product Innovation Award winners Acorn Scaffolding (Yorkshire) Ltd and highly commended TRAD Scaffolding Co Ltd – who the judges felt stood out in the competition.”
SMART Scaffolder launches a new website
CADS SMART Scaffolder launches a new responsive website.
SMART Scaffolder, the scaffolding software for scaffolders, has just launched an entirely new website. The Dorset based software firm say, the new website was designed right from the outset with mobile telephones in mind. “Knowing that most scaffolders spend much of their day on the road or on site it was important that our website is easy to read and it’s easy to find what you want on a smart phone” a spokesperson said. Ian Chambers, Sales & Marketing Director at SMART Scaffolder, said “We are very pleased that we have a modern website that is as easy to use as our software solutions”. The website also includes a new video that explains the benefits of the estimating, design and TG20 compliance software in under two minutes through the eyes of one of their customers, Ducker & Young Scaffolding. The film quickly shows how the software benefits scaffolders from setting out the scaffold to producing a professional looking quote, drawings and a materials list. SMART Scaffolder spokesperson added: “The ‘responsive’ website also provides more than a quick overview of the software and has a real depth of useful information. You can find out about the various product modules, get online help, read about TG20:13 or check out who’s who in SMART Scaffolder. There are also a number of testimonials from fellow scaffolders so you can see what they think of the software in their own words”.Malvern Key-Tie offers innovative new scaffold tie
Necessity has proved to be the mother of invention for Malvern, Worcestershire based Malvern Scaffolding Ltd. (Malvern).
Having got past the tender stage for a £700,000 retirement village scheme with the Wates Group, which was priced in 1.5m progressive masonry lifts, it soon became clear that some innovation would be required.
Malvern’s tender was based on the assumption that the scaffold would be tied through the window openings. However, Wates’ project manager wanted to install windows while the scaffold was still at full height for roofing.
Malvern contacted ADI Supply Ltd. (ADI), a specialist in a wide variety of scaffold fixings, which agreed to work with Malvern in finding a solution. Striving to avoid drilling, Malvern with ADI attempted a brickie installed slide lock tie, which was rejected by Wates because of cold bridging concerns, and a tang type tie, the first of which fixed to the inner blockwork and the tang to the outer brickwork; both failed the pull test.
Developing the tang concept further Malvern and ADI came up with what was to become the, “Malvern Key-Tie.” The tie is essentially a hook fitting welded on to a bar with a plate welded at the end. The brickie prepares a putlog type joint, the tie plate is inserted behind the external brickwork and then turned to lock it off, then it’s a case of attaching the scaffold to the hook. Removal is the opposite process.
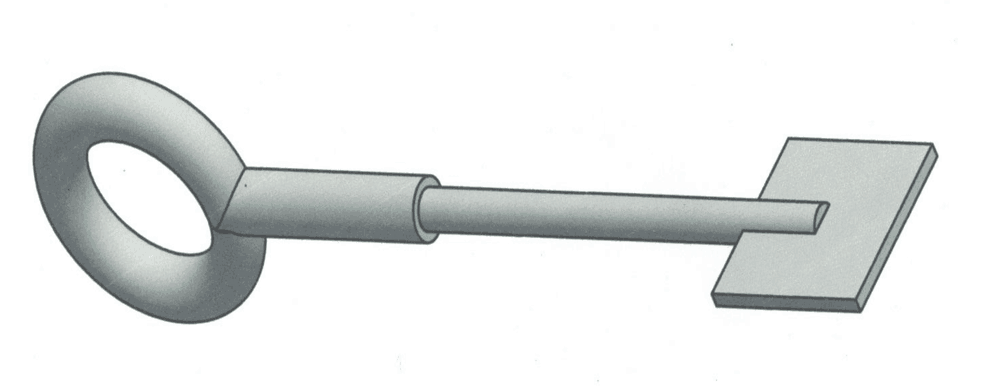
“The new ties are really quick to install through the slot the brickies leave behind,” said Jon Stone, Malvern’s commercial director. “There’s no drilling needed, no messing around in window openings. Just insert – lock – secure.
The scaffold is secured as in TG20 & TG4 using a hook fitting, but without the risk of damaging the front of the bricks, or having to relocate the ties once the windows need fitting. You can simply “fit and forget” and then retrieve them as the scaffold is stripped.”
Bearing in mind that compliance for most progressive masonry jobs requires a tie of around 2.5kN Malvern say that the Malvern Key-Tie was tested in-situ to 9kN and pull tested to destruction at 12.5kN. This was sufficient said Malvern to rate the Malvern Key-Tie for standard duty at 6.1kN thus covering the majority of applications.
Stone said the current version of the tie works within the around 40mm space cavity between the outside skin and the insulation, which give the Malvern Key-Tie the space to turn. However, Stone also said that Malvern has used the Malvern Key-Tie where the insulation board takes up almost all of the cavity and the tie has performed well too. “It (the tie) doesn’t penetrate the insulation board,” said Stone.
There is a bit of an education process prior to using the Malvern Key-Tie explained Stone but once the brickies understand what they have to do in order for the tie to work, “brickies have been great,” he said.
We asked if Malvern had experienced any significant labour saving through using the Malvern Key-Tie and while Stone said that the company had not performed any time and motion study yet he said that the company estimated that on a 100m perimeter building that four or five hours could be saved using the Malvern Key-Tie compared to drilling and about half of that with using window ties.
“The contractor is so much happier with the end product,” said Stone. He said that the tie has also performed well on existing buildings too but the ability to use the tie is strongly dependant on the type of cavity that is present.
“We have entered the Malvern Key-tie as a new innovation in the NASC New Product Awards. We know we are up against some stiff competition but most of the other contenders are either system based or only used in special circumstances, whereas the new Malvern Key-tie can be used in numerous situations and will be of use to every scaffold firm in the country.
It is not just new builds either, most modern buildings have a cavity where the Malvern Key-tie can be used,” said Stone.
Eight entries shortlisted for the NASC Scaffolding Product Innovation Award
- Acorn Scaffolding (Yorkshire) Ltd (Creamfields Steel Yard temporary event venue)
- Malvern Scaffolding Ltd (the ‘Malvern Key-Tie’)
- TRAD Scaffolding Co Ltd (a new/revolutionary Gin Wheel)
- Layher Ltd (new Universal Aluminium HD Beam)
- HAKI Scaffolding Ltd (HAKI Decking CADEE system)
- TRAD Hire & Sales Ltd (Plettac Metrix Permanent Advanced Guardrail)
- GKR Scaffolding Ltd (Elimin-8 innovative scaffold fitting)
- Focus Scaffolding Ltd (two and three board hop-up bracket for tube and fitting)
CN Specialist Awards finalists announced
The best of the best from the UK scaffolding fraternity will go head-to-head at the Construction News Specialist Awards 2017 after finalists are announced.
The Construction News Specialist Awards is in its 13th year and celebrates the achievements of the best specialist contractors in the UK. The awards are a fantastic opportunity for contractors to position themselves as leaders within their industry and receive recognition for their outstanding work. Out of all the many entrees, Six industry recognised scaffolding and access firms have been shortlisted, they will be battling it out in the following categories: Access and Scaffolding Specialist of the Year Finalists- This category aims to recognise the best access and scaffolding specialist contractor in the industry.- Artel Scaffolding (NASC Members)
- GKR Scaffolding (NASC Members)
- JECS Offshore Scaffolding
- TIGER Scaffolding (Scaffolding Association Members)
- WellMax Scaffolding (Scaffolding Association Members)
- Klawz: Klawz Scaffolding Fitting (Scaffolding Association Members)
- TIGER Scaffolding (Scaffolding Association Members)
- GKR Scaffolding (NASC Members)
“We are absolutely delighted to see a number of our members shortlisted across a range of categories at the CN Specialist Awards. To see them being recognised at a prestigious event like this truly demonstrates the commitment that they have to raising standards and improving the image of the industry.”Each entrant has their work assessed in front of a panel of distinguished clients, industry leaders and construction experts, and after submitting their initial entry online the shortlisted entrants will next be delivering a face-to-face presentation to a judging panel in January. The winners will be announced at the awards evening at the Grosvenor House Hotel, London on the 22nd March 2017.
MTD Scaffolding gains NASC accreditation
MTD Scaffolding becomes one of the NASC’s newest members
MTD Scaffolding has announced they have successfully gained membership status of the NASC (National Access & Scaffolding Confederation) Given the NASC strict membership criteria, MTD say gaining the reputable accreditation is an achievement.
MTD Scaffolding is a Midlands-based scaffolding company, with three depots in Telford, Loughborough, and Oldbury. The firm provides system and traditional scaffolding for public and private projects. MTD recently received major financial support from the Altrad Group, to invest in developing the business and train its scaffolders. The business has a view to move into new sectors – new build, commercial, railway, highways, and waterways. It also aims to secure larger construction projects alongside social housing contracts.
“We are thrilled that NASC has accepted MTD Scaffolding to join its impressive membership base, the opportunity to grow our business from this accreditation and break into more market sectors means that the future for MTD will be both exciting and challenging” said Sarah Vanes, Operations Director of MTD. “Our business has over 30 years’ experience, and a great reputation within the industry. It’s a real achievement for the company, its staff and operatives to gain the NASC accreditation from the premier scaffolding trade body,” she said.
To the join NASC, a company must meet a set of stringent membership criteria which include from the initial application, a desktop audit of the application, a visit to the companies premises to verify the information received, followed by site visits to audit on site practices which the NASC auditors place a great emphasis on. Audits including sites are then carried out on a biannual basis to ensure continued compliance.
NASC members must also attend two NASC meetings each year, and abide by a comprehensive code of conduct.
“Being an NASC member is imperative in this industry. These days, most main contractors and public authorities will only hire NASC-accredited suppliers,” Sarah said. “Our NASC accreditation assures our customers that we are a reputable company that meets strict standards and always puts safety first.”
NASC report ‘Boom Time’ with surge in memberships
The NASC have just recently launched their 2017 Yearbook announcing the confirmation of the highest level of NASC membership, since their formation in 1945.
NASC Managing Director, Robin James opens the 2017 Yearbook with a welcome note stating: ‘It’s boom time for the NASC and its members’ – as membership enquiries and applications peaked, sales of the widely accepted TG20:13 soared and the value of NASC membership reached scaffolding companies of all sizes in 2016.
Over the past 12 months the NASC has been out on a membership drive to attract more small and medium sized scaffolding businesses, after NASC President Alan Lilley launched the campaign in Leeds at the 2015 AGM.
Alan Lilley said: “I am pleased to report the initiatives we undertook to attract new members have proved an unqualified success.”
“I am eager for the NASC to be seen to represent the whole of the scaffolding industry and further initiatives by the confederation are being planned to broaden its appeal. Now is an opportune time to apply for contracting membership.”
The NASC’s widely respected 2017 Yearbook also contains updates on new and revised NASC guidance, CISRS training and Britain’s premier access and scaffolding projects, as well as details of the activities of the confederation in 2016.
NASC Managing Director, Robin James added: “The NASC 2017 Yearbook testifies to a healthy and dynamic industry, and one that continues to astonish and amaze. The range and quality of work carried out by NASC member companies simply underlines the importance of maintaining the highest possible standards where requirements for NASC membership are concerned.”
ScaffMag features on Have I Got News For You
St Helens Plant wins 2016 Build Awards
Merseyside based St Helens Plant have won the Construction and Engineering category plus an ‘Excellence Award’ for Scaffolding Fabrication, Repair and Reconditioning’ in the recent Build Awards 2016.
This is the second high profile accolade in 2016 for the NASC full non contracting (hire/sales) member – known within the industry for their fabrication, repair and reconditioning services. St Helens Plant were also awarded a finalist placement in the Access and Scaffolding Specialist of the Year category in the Construction News 2016 Specialists Awards in February.
In a recent press release from the NASC St Helens Plant was reported to be one of the UK’s all-encompassing scaffolding supply specialists, the firm has gained national and international recognition for their commitment and contribution to the access and scaffolding industry.
Gordon Pilling of St Helens Plant said: “We’re delighted to have been nominated by our clients, and to have won this construction and engineering award, also to have gained an excellence award for scaffolding fabrication, repair and reconditioning.
“It’s another award purely down to the strength, commitment and loyalty of each one of our team, from factory, dispatch and delivery, and office staff. We are very proud of all of who commit daily to St Helens Plant and have made our international recognition and awards possible. I extend my gratitude to our clients and the Build Awards for the privilege of being awarded this accolade.
“Safety of supply is a huge focus for us at St Helens Plant and being part of NASC, we try and promote this as much as we can at every opportunity.”
NASC MD Robin James added: “Congratulations to St Helens Plant on this magnificent achievement for their services to the scaffolding sector. Working alongside big clients in the scaffolding industry, expanding their operations and winning significant awards, they are living proof of the success NASC members have had in 2016. We wish them further success into 2017 and beyond.”